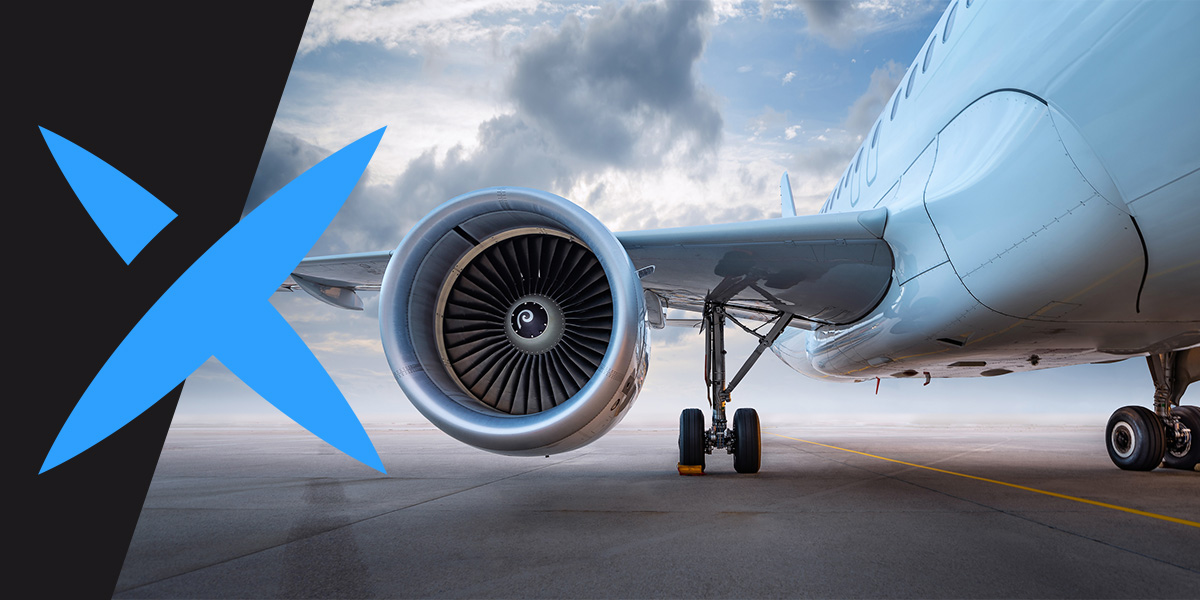
Best Blast Media for Airplane Parts
Abrasive blasting is an effective method for removing coatings, corrosion or cleaning up an airplane’s parts. However, like with any blasting project, choosing a suitable abrasive is perhaps the most important part, as you must consider the surface being blasted and the reason for blasting.
For aviation purposes, many blasters recommend using an abrasive on the softer side, like crushed walnut shells, corn cobs, or plastic beads. However, a new class of abrasives — superoxalloy — can offer significant advantages over traditional blast abrasives in many aviation and aerospace applications.
Types of Blast Abrasives for Aircraft Parts
Harsh abrasives like aluminum oxide, or garnet may negatively impact the surface being blasted. Using a harder abrasive helps remove layers of paint or corrosion more quickly, but there’s a risk that the underlying surface may become over-profiled or warped.
With a softer media, the amount of energy being applied to the surface won’t be as high, and there’s less risk of damaging the material. However, the downside to this is that the process itself will likely not go as quickly as with a harder abrasive.
Media like aluminum oxide, silicon carbide, and garnet are also more likely to leave embedded particles in the surface. Unfortunately, this can lead to quality issues or leave an undesirable texture, making it difficult to apply the proper coating.
What’s the Best Media to Use for Airplane Parts?
Superoxalloy abrasives are a better option for aircraft part blasting because they don’t damage the underlying material, but they still work quickly. This type of abrasive has been engineered through controlled formulation to create tempered non-crystalline particles that resist breakage and last through many uses.
In addition to their strength, superoxalloys are also safer for employees and the environment. 10X Superoxalloy is produced from the by-product of mineral wool insulation, making it the industry’s most safety-tested abrasive material. No other blasting abrasive has achieved 10X superoxalloy’s validated high level of safety for people, air, water, and wildlife. Read our dedicated safety page to learn more. Of course, employees should always wear protective OSHA-required PPE, including a forced air respirator, when working with a sandblaster, regardless of the material being used.
Also, unlike many other abrasives, superoxalloys don’t leave embedded particles behind in the part’s substrate. This makes it much easier to coat aircraft parts with protective coatings.
Choose Superoxalloy Abrasives From 10X Engineered Materials
At 10X Engineered Materials, we’ve created an all new category of engineered blasting abrasives that outperform traditional blast media. Our EpiX abrasive line is designed for precision projects and is in use for many aviation maintenance processes.
You can find our abrasive blast media at distributors around the U.S., and Canada, or order our EpiX line directly from our website. To find out more, call us at 260-253-2278 or fill out our online form.