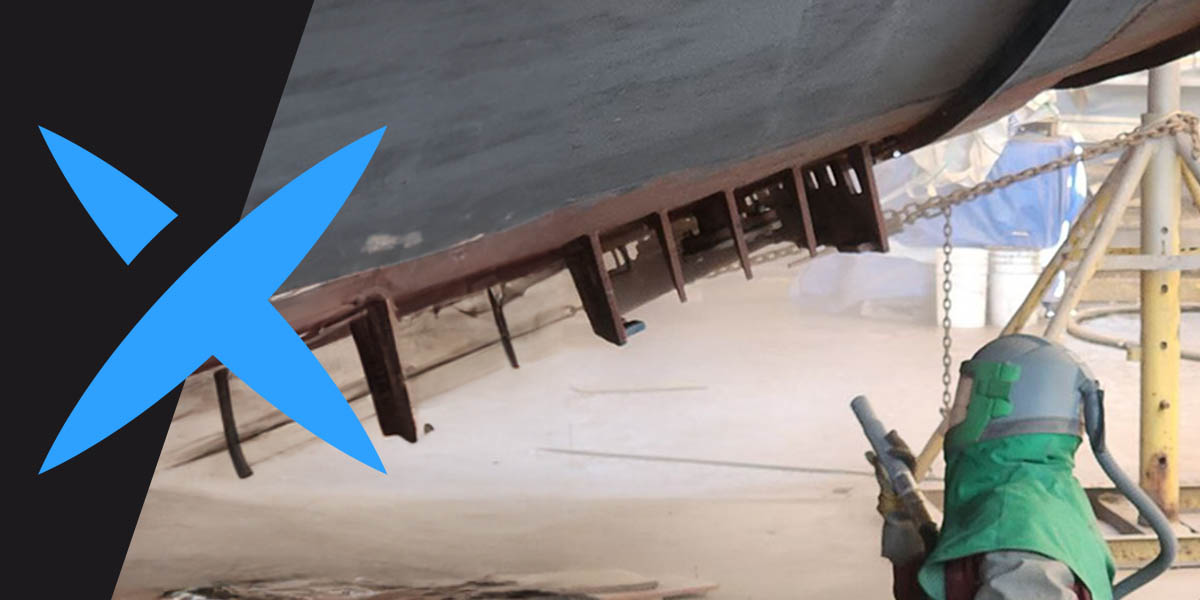
When it comes to sandblasting equipment, each component matters. From the nozzle tip to the inner diameter of the blast and air supply lines and the rating of your air compressor to the abrasive media, each piece of your blasting system plays a role in your productivity and efficiency. This comprehensive nozzle selection guide explains everything you need to know about choosing the right component for your specific application.
How Does a Blast Nozzle Work?
Sandblasting uses several connected equipment and components:
- Air compressor
- Air dryer
- Connection air hoses and/or pipes
- Pressurized abrasive blast pot
- Abrasive metering valve
- Blast hose
- Nozzle blast control handle or deadman switch
- Abrasive blast nozzle
Blasting nozzles are straightforward and easy to use. When depressing the nozzle deadman switch, you release the abrasive and compressed air together in a high-speed stream. The air and abrasive are accelerated through the nozzle and hit the surface with enough force to blast away any coatings, corrosion or other unwanted surface residues.
As a general rule, you will want to choose a nozzle with an orifice size that can achieve at least 100 psi of pressure (measured near the nozzle), given the air volume and pressure capacities of your air compressor. Air compressors are rated for an air flow in cubic feet per minute (CFM) at its maximum design pressure (psi).
How Do You Choose a Blast Nozzle?
There are several things to consider when choosing a nozzle suitable for a specific job.
1. Compressed Air Supply
The rated flow and pressure capacity of your air compressor is an important factor in deciding which nozzle you should use for your project.
It is important to remember that your air supply system powers more than the nozzle. It also supplies compressed air to components such as the:
- Pneumatic controls
- Air motors
- Forced air blast hood
As you attach more hoses and nozzles to your blast pot, the amount of air you will need to blast at the required pressure increases. Ultimately, no matter how many nozzles you use, you will want to choose a size that allows for maximum blasting productivity while staying within the capabilities of the air compressor.
Generally, a smaller nozzle will create a narrower blast pattern that consumes less air. As you increase the orifice size of your nozzle, the blast pattern will widen and air consumption will increase. Nozzles that are too large will exceed the capacity of your air compressor, leading to a decrease in air pressure and significantly reduced productivity.
2. Nozzle Wear
Over time, abrasive media will wear down the inside of your nozzle. This wear will increase the orifice, which will increase the compressed air volume required to maintain the desired nozzle pressure.
The required air flow at a given nozzle is proportional to the square of the orifice diameter. For example, if you double the orifice of your nozzle over time, you will quadruple the required compressed air volume to achieve the same nozzle pressure.
Increased compressed air volume causes increased pressure drop throughout the system. What happens in practice is that the pressure at the nozzle decreases as the nozzle wears and the orifice size increases, which will negatively impact blasting efficiency. Increased nozzle orifice size can also cause the air demand to exceed the capacity of the air compressor, which will cause the pressure throughout the blast system (compressor, pot and nozzle) to decrease.
Nozzles should be checked for wear frequently to prevent unnecessary losses in productivity. The size of the orifice opening can be measured using an orifice gauge. When the opening is 1/16 of an inch larger than the listed orifice size for the nozzle, the nozzle should be replaced.
3. Bore Shape
Blast nozzles come in two main shapes — straight bore and Venturi. Each type has multiple subtypes that create different blast patterns and particle acceleration for different blast jobs. Here is how some of the more common shapes break down:
- Straight bore: A straight bore nozzle is effective for spot blasting, blast cabinets or other high-precision applications due to its tight blast pattern.
- Venturi: A long Venturi blast nozzle has a narrow throat and a large exit opening, which increases the pressure and creates a wide, high-velocity blast pattern. This nozzle shape is ideal for larger-scale projects where you need aggressive blasting.
- Double Venturi: These Venturi nozzles add an air gap at the exit end, which allows you to produce larger blast patterns and are ideal for mill scale removal blasting applications.
- Angle bore: Angled nozzles are ideal for efficiently blasting hard-to-reach spots and cavities on a workpiece.
- Wide throat: The large throat and wide opening create a wide blast pattern that can provide up to a 15% increase in productivity over nozzles with a smaller throat.
4. Nozzle Material
Abrasive blaster nozzles come in several different materials, each with its own advantages and disadvantages.
- Ceramic: Ceramic is a traditional material for blast nozzles that performs well with softer abrasives. However, it wears down quicker than other materials — especially when paired with a harder, more angular abrasive media.
- Aluminum oxide (alumina): This material is slightly more durable than ceramic, with a good service life in low-usage settings.
- Tungsten carbide: Tungsten carbide is a popular nozzle material due to its high durability and impact resistance, which makes it a solid choice for applications requiring a more aggressive sandblasting grit and harsh blasting environments.
- Silicon carbide: Although silicon carbide nozzles have a life span rivaling that of tungsten carbide, they are lighter and more suitable for applications where operators will spend long hours blasting a workpiece. However, they have lower impact resistance and are susceptible to cracking or shattering if dropped.
- Boron carbide: If you are looking for the longest-lived nozzle material, boron carbide is a good choice. Its high wear resistance means it can withstand extended use of aggressive abrasive media, and it is highly resistant to impact.
The factors affecting nozzle material selection are primarily durability and cost, but weight and personal preference also factor into what may be best for your project.
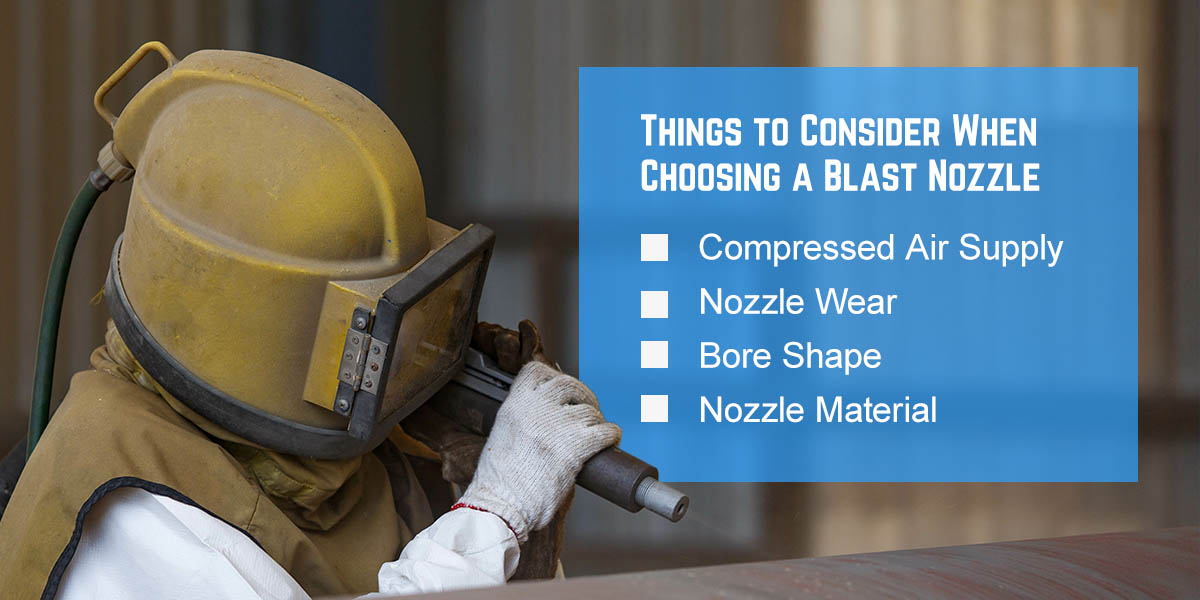
Selecting a Nozzle Size for Your Application
Nozzle size selection is primarily driven by the requirements of the blast job. Generally, smaller nozzles are used for small parts or precision tasks, often in a blast cabinet.
For industrial-scale jobs, such as tanks, pipelines or ships, using larger nozzles will dramatically improve blasting efficiency, provided that the air compressor has sufficient capacity and connection and blast hoses are properly sized.
In addition, the larger the nozzle, the higher the thrust force on the blaster at a given blast pressure, so the blaster may need to be trained on how to brace the nozzle against his or her body to prevent exhaustion and enable ergonomic blasting.
The most common blasting nozzle sizes range from 1/4 inch (#$) to 5/8 inch (#10) orifice opening, increasing by increments of 1/16 inch. Once you know your air compressor specifications, abrasive media, and nozzle pressure, you can decide on the nozzle size you need for the job. Here, we have outlined the general ranges for each of the most common nozzle sizes for your convenience.
Note that your actual numbers will vary depending on your equipment’s condition and configuration as well as the specific type of abrasive you use. If you have trouble deciding what size nozzle to use in your sandblasting application, it can help to seek guidance from the nozzle manufacturer, equipment supplier or abrasive supplier.
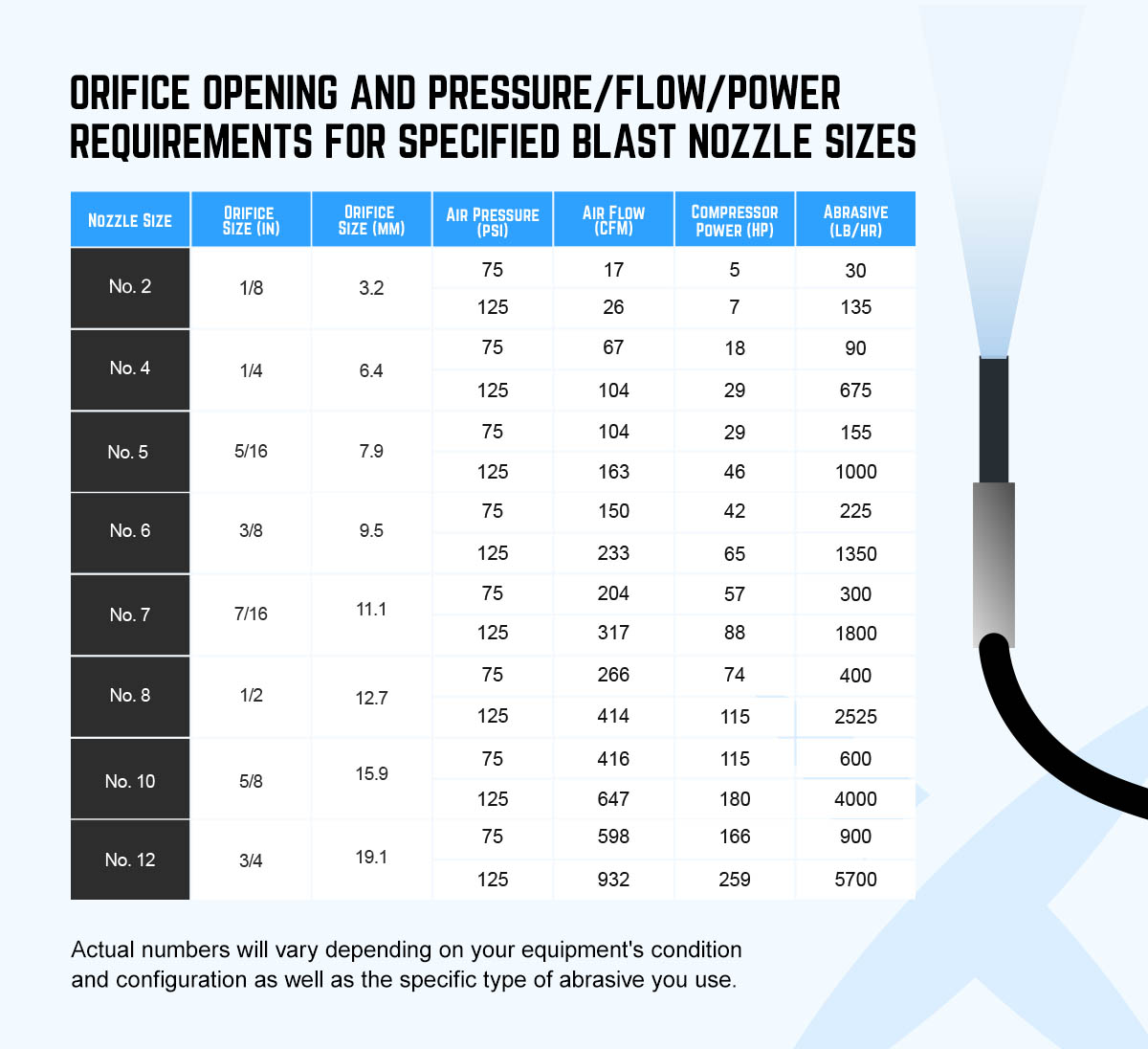
#2: 1/8 Blast Nozzle
As the smallest nozzle size, #2 (3.2 millimeters) blast nozzles will produce the narrowest blast patterns. This makes them ideal for spot blasting and other localized tasks on smaller workpieces.
A typical 1/8 inch blast nozzle will require:
- Air flow: 17 to 26 CFM
- Air pressure: 75 to 125 psi
- Compressor power: 5 to 7 horsepower (HP)
- Abrasive: 30 to 135 pounds per hour (lb/hr)
#4: 1/4 Blast Nozzle
While it will still be quite narrow, a 1/4-inch (6.4 millimeters) nozzle will create a slightly wider blast pattern than a #2 nozzle. This blast pattern makes it suitable for small, precise applications like automotive detail work or molding weld seams in equipment manufacturing.
The typical operating ranges for a #4 blast nozzle include:
- Air flow: 67 to 104 CFM
- Air pressure: 75 to 125 psi
- Compressor power: 18 to 29 HP
- Abrasive: 90 to 675 lb/hr
#5: 5/16 Blast Nozzle
As the nozzle size increases, pressure and velocity naturally decrease at a given compressed airflow.
The average requirements for a #5 (7.9 millimeters) blast nozzle include:
- Air flow: 104 to 163 CFM
- Air pressure: 75 to 125 psi
- Compressor power: 29 to 46 HP
- Abrasive: 155 to 1,000 lb/hr
#6: 3/8 Blast Nozzle
A #6 nozzle (9.5 millimeters) will typically be suitable for a wide range of blasting applications, including both detail work and surface cleaning.
The normal operating ranges for this sandblasting nozzle orifice size includes:
- Air flow: 150 to 233 CFM
- Air pressure: 75 to 125 psi
- Compressor power: 42 to 65 HP
- Abrasive: 225 to 1,350 lb/hr
#7: 7/16 Blast Nozzle
#7 (11.1 millimeters) nozzles are effective for large-scale applications like cleaning and coating removal from larger surfaces, such as on ships or tanks.
Typical operating requirements for this nozzle size range from:
- Air flow: 204 to 317 CFM
- Air pressure: 75 to 125 psi
- Compressor power: 57 to 88 HP
- Abrasive: 300 to 1,800 lb/hr
#8: 1/2 Blast Nozzle
Larger nozzle sizes produce wider blast patterns, making them more suitable for large-scale applications like bridges, railways, and pipelines. Regardless of shape, these nozzles will allow you to get more done in less time — and the higher efficiency can also allow you to cut operational costs by reducing the amount of abrasive you consume per square foot of blasted surface. A larger nozzle can also decrease the time to complete jobs, compress the overall project schedule, and decrease all time-based costs like labor, equipment rental, and fuel consumption.
Generally, a 1/2-inch (12.7 millimeters) nozzle will require:
- Air flow: 266 to 414 CFM
- Air pressure: 75 to 125 psi
- Compressor power: 74 to 115 HP
- Abrasive: 400 to 2,525 lb/hr
#10: 5/8 Blast Nozzle
As one of the largest nozzle sizes, a #10 (15.9 millimeters) nozzle will be best used for clearing broad surfaces quickly and efficiently. It is unsuitable for small-scale applications where precision is essential. The thrust force on the blaster will be quite large at normal operating nozzle pressure (~100 psi). Blasters should be trained to brace the nozzle using their bodies to blast ergonomically and avoid fatigue.
Requirements for optimal operation include:
- Air flow: 416 to 647 CFM
- Air pressure: 75 to 125 psi
- Compressor power: 115 to 180 HP
- Abrasive: 600 to 4,000 lb/hr
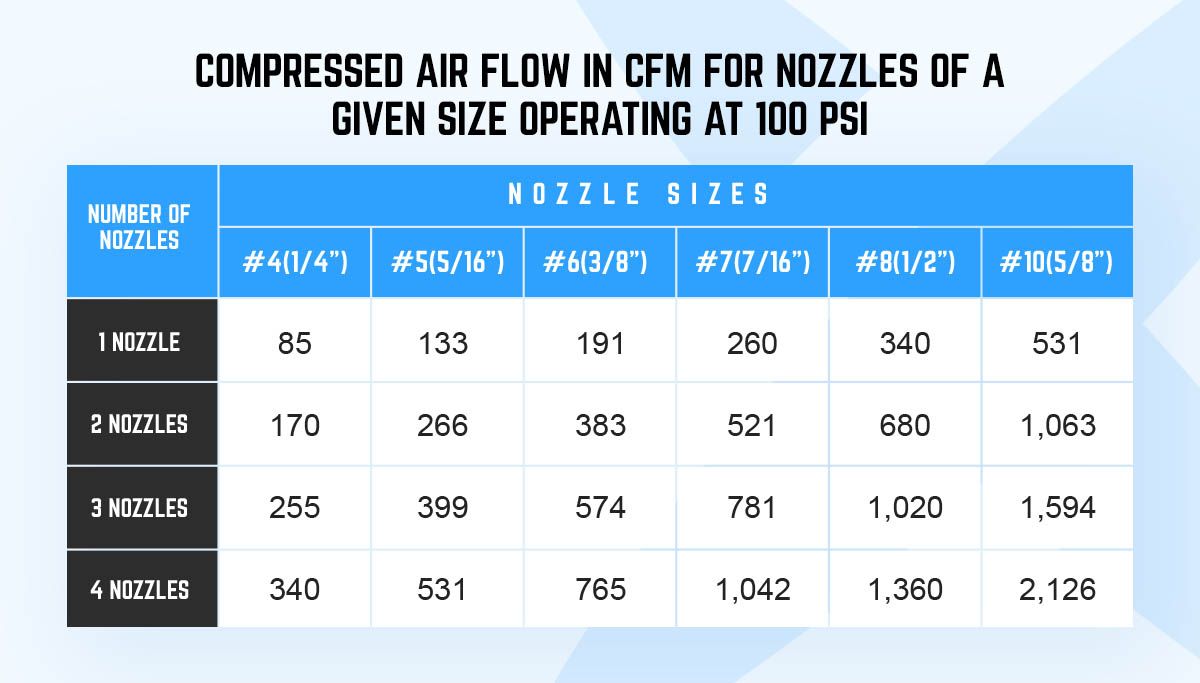
Why Choose Superoxalloy Abrasives From 10X Engineered Materials?
Whatever size blast nozzle you need, our superoxalloy abrasives will push your next sandblasting project to the next level of quality and efficiency.
Unlike traditional abrasives, which have an angular or sub-angular shape, superoxalloy abrasives have all particle shapes. They are also tempered and amorphous, which makes them exceptionally tough and reduces their likelihood of shattering on impact.
Our EpiX abrasives are ideal for high-efficiency manufacturing and fabrication projects where lower blast profiles and surface quality is paramount. You can create a clean, finished surface in just one step — without dealing with burn-off, scraping or iron contamination.
For larger production and maintenance jobs, choose our DynamiX or KinetiX superoxalloy abrasives. With delayed rust bloom and minimal embedment, these abrasive products allow you to deliver high-quality results within tight timelines while reducing your overall abrasive consumption.
All of our abrasive product ranges are compatible with a wide range of nozzle sizes and materials, so you can easily match your equipment to each project’s unique specifications.
Order 10X Abrasives Today
At 10X Engineered Materials, our goal is to enable transformational improvements in quality and productivity for any sandblasting application. Contact us online or give us a call at (260)-253-2278 to discuss your requirements with one of our knowledgeable sales reps. We will help you decide which 10X abrasive is the best fit for your blast nozzle size and application.