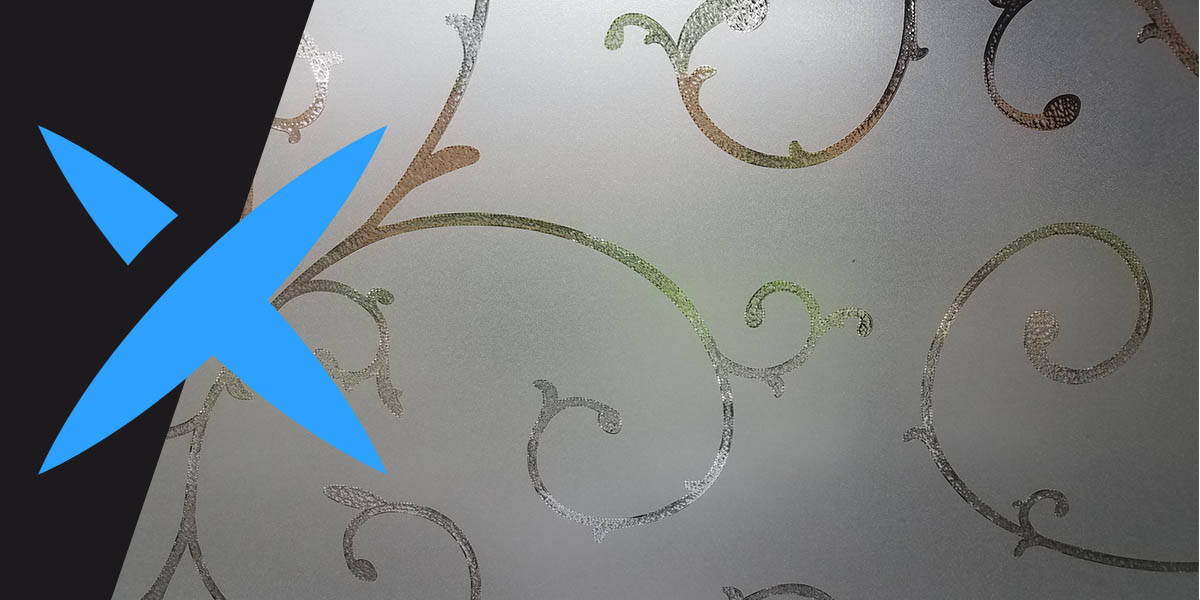
Sandblasting is traditionally used to remove corrosion, contaminants and coatings but can also serve other purposes. This technique is also a versatile and effective glass etching method with various artistic and practical possibilities.
Sandblasted glass looks frostier compared to non-blasted glass areas. It can be used to decorate or customize small pieces like drinking glasses. It can also create privacy while still allowing natural light to enter areas like meeting rooms. Sandblasting is an effective and creative way to reconfigure glass, offering precision and flexibility in its design and execution.
Learn more about etching glass with sandblasting, including how to frost glass with a sandblaster and the recommended materials, equipment and abrasives.
Understanding Sandblasting
Sandblasting is primarily used to prepare workpieces or surfaces for coatings or additional finishing steps before coating. It uses a high-pressure stream of abrasive material to clean or etch surfaces. These materials are typically sand, glass beads, aluminum oxide, or silicon carbide, which often negatively impact the environment and workers’ health. Superoxalloy abrasives are a great alternative with better economics and the best safety profile on the market.
Can You Sandblast Glass?
Yes, sandblasting is used on doors and windows to create decorative glass panels, office partitions, glass shower doors, and signage. Using the right sandblasting material for glass etching offers the following benefits:
- Durability: Etched glass created with sandblasting is resistant to wear and fading, making it ideal for both decorative and functional applications.
- Versatility: Sandblasting can be used to etch various glass surfaces, including curved surfaces, flat panels and glassware.
- Precision: Sandblasting gives you precise control over depth and detail, allowing you to create intricate patterns on the glass.
- Customization: Sandblasting glass simplifies customization options, like using stencils to personalize the piece with logos or names.
- Matte finish: You can frost glass with a sandblaster, creating a smooth, matte surface finish and giving the surface a textured appearance.
Essential Glass Sandblasting Equipment
When etching glass with a sandblaster, using the right equipment is vital to ensure you achieve the intended results. Some essential pieces you will need for glass sandblasting include:
- Sandblasting cabinet: A sandblasting cabinet contains the sandblasting process, preventing the materials from scattering. A cabinet designed for glasswork will include special lighting and windows that allow you to monitor the progress.
- Blast gun: The blast gun directs the abrasive material flow, allowing for precise control over the etching area.
- Air compressor: The air compressor powers the blast gun, giving it the air pressure needed to propel the abrasive material onto the glass surface.
- Stencil material: For detailed designs, vinyl or rubber stencils help mask parts of the glass that should not be etched.
- Protective gear: Safety is essential in sandblasting. Workers should wear protective gear like goggles, gloves, and respirators to protect their lungs from dust and airborne abrasive particles.
How to Etch Glass With a Sandblaster
Sandblasting glass creates a rougher, textured finish on the substrate. The technique is used for texturing, etching designs, frosting, and creating decorative art. The surface may have slightly less uniformity but a consistent finish. It is very durable and can withstand harsh cleaning agents and weather conditions.
You can use several types of glass to etch with sandblasting. These include:
- Float glass like window glass.
- Tempered glass — you can sandblast tempered glass.
- Annealed glass, including mirror glass.
- The outer layers of laminated glass.
- Colored or stained glass, including artistic glass.
- Textured glass.
Tempered or laminated glass is preferable for outdoor settings to ensure the project’s longevity in harsher environments. However, using a damp cloth and mild detergent to clean the surface gently is still relatively easy to maintain.
The Glass Etching Process Overview
Use these steps as a general guide when etching glass using sandblasting:
- Clean the glass surface with glass cleaner to ensure it is completely free of contaminants like dust and oils.
- Apply a stencil or use masking tape to cover areas that should not be etched. Ensure it adheres well to prevent abrasive material from getting underneath.
- Hold the sandblaster to the glass surface at a consistent 45-degree angle with 20 to 30 psi air pressure for light etching and 40 to 70 psi for sand carving.
- Keep a steady distance from the glass and move the sandblaster in a smooth, even motion across the areas you want to etch. Avoid staying in one spot for too long to prevent over-etching.
- Periodically stop to check the progress and ensure the etching is even and as deep as needed to suit your design.
- Take off any stencils and clean the glass again after etching to remove any residual dust.
How Do You Sandblast Glass to Make It Frosted?
Frosting glass with a sandblaster involves blasting the entire or most of the surface with abrasive material to create a translucent, frosted appearance. The process involves the same steps as etching glass with sandblasting. When you are done, it is important to check that the frosting is even and consistent and meets your expectations.
Recommended Sandblasting Abrasives
EpiX MP and LP is 10X Engineered Materials’ answer to etching glass with sandblasting. These blasting abrasives will not shatter glass when used at lower pressures. This patented solution decreases processing time, significantly reduces dust, and is cost-effective. These products offer high-quality results with virtually zero embedment.
1. EpiX MP Superoxalloy Abrasive
EpiX Medium Profile (MP) has a uniform, medium profile that produces a clean, frosted finish. It is a good choice if your operations need an 80-, 90- or 100-grit aluminum oxide.
2. EpiX LP Superoxalloy Abrasive
The EpiX Low Profile (LP) produces uniform, low-profile frosted finishes. It replaces your 150- and 180-grit aluminum oxide, silicon carbide, garnet, glass beads, and more.
Elevate Your Sandblasting Projects With 10X Engineered Materials
Sandblasting is a technique favored for its precision and ability to produce customized artwork. Etching glass with sandblasting is a popular, versatile technique used to create intricate patterns and designs on glass surfaces. Whether you are new to the industry or have run your business for years, sandblasted glass can elevate your glass projects to a new level of sophistication.
At 10X Engineered Materials, we help you optimize your blasting system with the unique properties of superoxalloy abrasive particles. They will deliver a higher-quality finish than other products. We also offer free technical support to help your operations run smoothly and efficiently.
Make an engineered decision today and order your EpiX products online, or contact our team of professionals for more information.