The safety of materials like slag is a pressing concern in abrasive blasting and industrial cleaning. While these materials are highly effective, slag poses health risks, including respiratory and carcinogenic hazards. Understanding the hazards associated with slag is essential before implementing safer practices or, ideally, selecting an abrasive media that is safer for both workers and the environment.
Understanding Slag
Due to its angularity, hardness and high density, slag is an abrasive material extensively employed in surface preparation and industrial cleaning processes. Derived as a by-product of metallurgical operations, especially copper slag, which forms during the smelting of ferrous and nonferrous metals, slag possesses the requisite mechanical characteristics to effectively remove coatings, rust and contaminants from metallic substances.
Coal slag comes from coal combustion processes in power plants. Nickel slag is a by-product of the nickel smelting process, where nickel metal is extracted from ore. The impurities separate to form the slag.
Industrial users favor slag for its versatility across multiple applications, from pipeline restoration to shipbuilding and maintenance. It is available in various gradations, allowing customization to meet specific project requirements like Near-White Metal Blast Cleaning (SSPC-SP10 or NACE No.2).
Health Risks Associated With Exposure to Slag
Due to their chemical composition and physical properties, slag abrasives pose various health risks. The specific risks depend on the type of slag, such as coal, copper, or another by-product.
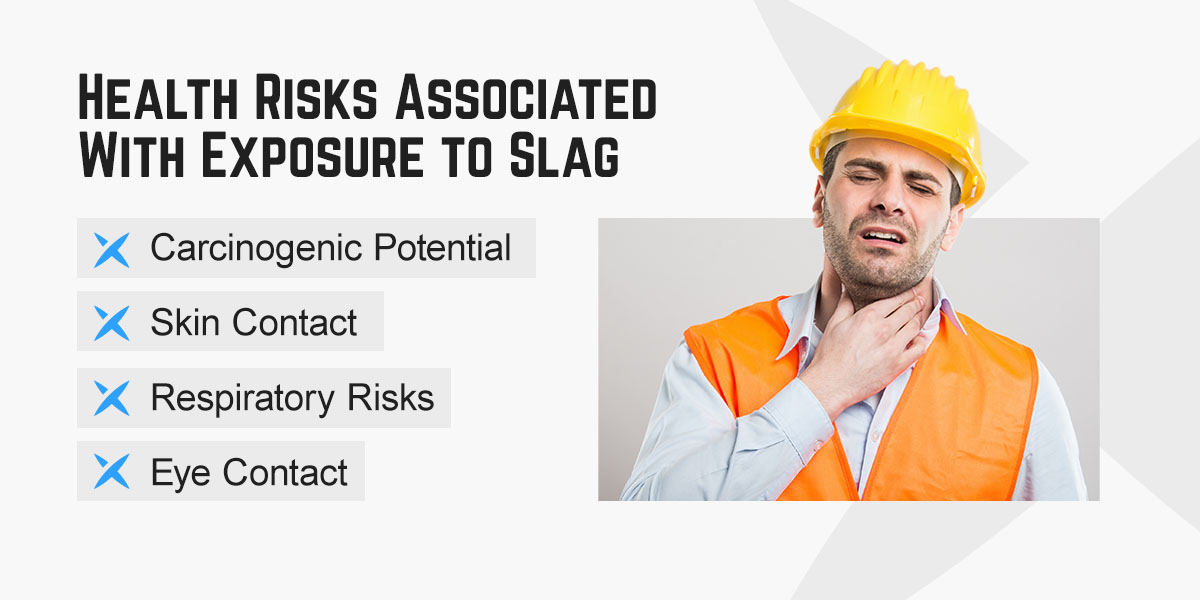
Carcinogenic Potential
Slag’s carcinogenicity is a significant concern, especially with coal slag. It often contains crystalline silica. Prolonged inhalation of this crystalline silica dust can lead to silicosis, a lung disease that increases the risk of lung cancer. The International Agency for Research on Cancer classifies this substance as a Group 1 carcinogen, meaning slag is carcinogenic to humans.
Skin Contact
Slag is generally safe to touch as it is not considered acutely toxic upon skin contact. However, its highly abrasive nature can cause mechanical irritation, such as cuts or abrasions. Additionally, the presence of other hazardous substances may lead to dermal absorption over time, though this is typically less of a concern compared to inhalation risks.
Respiratory Risks
When slag is used as an abrasive, the blasting process generates fine particulate matter, including dust, which is the primary health concern. Prolonged contact with this matter can result in:
- Acute effects: These include irritation of the respiratory tract, coughing and shortness of breath.
- Chronic effects: Long-term exposure can lead to conditions like chronic obstructive pulmonary disease and increase susceptibility to respiratory infections.
Eye Contact
Direct contact with slag particles or dust can cause irritation or mechanical injury to the eyes. In blasting environments, the fine, sharp-edged particles can be especially harmful if proper protective eyewear is not used. This is true of most types or abrasive blasting materials.
Environmental Impact
The extent of slag’s environmental harm depends on the type of slag, its chemical composition, and management practices employed during its life cycle:
- Heavy metal leaching: Slag from copper and coal sources contains trace levels of chromium, cadmium, and arsenic. It can leach into groundwater and soil, posing risks to ecosystems and human health.
- Residual waste: Post-blasting slag often contains removed surface materials like paint or rust in addition to its original constituents. If these coatings include substances like polychlorinated biphenyls, the resulting waste is classified as hazardous, requiring specialized handling.
- Radioactive contamination: Slags derived from ore with naturally occurring radioactive materials may exhibit low levels of radioactivity, which can persist in the environment.
5 Safer Alternatives for Abrasive Blasting
When considering alternatives to traditional slag abrasives, prioritizing safety, sustainability, and performance is crucial. Each option offers unique benefits and suitability for various industrial applications.
1. Superoxalloy
Superoxalloy is a cutting-edge abrasive material engineered for exceptional performance while prioritizing environmental safety and human health. It’s non-toxic, recyclable, and is the only abrasive on the market with a unique safety profile, primarily due to its classification by the International Agency for Research on Cancer (IARC) as a Group 3 material—“not classifiable as to its carcinogenicity to humans.”
This product represents the future of abrasive blasting, combining engineering with a commitment to health and safety protocols. Key benefits include:
- Durable: Its high durability allows for multiple reuse cycles, enhancing cost efficiency and reducing material consumption.
- Efficiency: With unmatched hardness and polymorphous particles, it delivers faster cutting speeds and higher productivity.
- Safe: Superoxalloy products generate less dust and are biosoluble in the lungs, making them safer for prolonged use.
- Versatile: Available in various grits, superoxalloy abrasives are suitable for a broad range of applications.
2. Crushed Glass
Crushed glass comes from post-consumer glass products like soda bottles. The material is crushed and cleaned to produce an inert, nontoxic abrasive media with the following benefits:
- Eco-friendly: Crushed glass diverts waste glass from landfills to support circular economy principles.
- Cost-effective: Crushed glass is readily available and inexpensive compared to many of the alternatives.
3. Walnut Shells
Walnut shell abrasives are organic media derived from crushed walnut shells, making them suitable for cleaning delicate surfaces. Their benefits include:
- Biodegradable: Walnut shells are completely organic and environmentally benign.
- Gentle: It’s ideal for composites, soft metals, and fragile substances.
- Renewable: This abrasive is sourced from agricultural waste, promoting sustainability.
4. Dry Ice
Dry ice blasting uses solid carbon dioxide pellets as the abrasive. It sublimates upon impact, leaving no secondary waste. Additional benefits include:
- Surface-friendly: Dry ice is gentle enough for sensitive equipment and other delicate substrates.
- Nontoxic: It’s safe for both operators and the environment, as it does not introduce contaminants.
5. Baking Soda
Sodium bicarbonate, or baking soda, is a biodegradable, water-soluble abrasive that is widely used for cleaning and coating removal, offering these benefits:
- Gentle abrasion: It is ideal for cleaning without damaging underlying surfaces.
- Water soluble: Baking soda easily washes away, simplifying cleanup.