Powder coating is a durable, environmentally friendly finishing process widely used in aerospace, automotive, architecture, and consumer goods industries. These coatings do not require solvents, making them more sustainable and efficient. The colors and finishes available for powder coating are virtually limitless and influenced by chemistry, application techniques, and environmental considerations.
Understanding formulation principles, color standards, and application techniques ensures optimal results for industrial and commercial projects, whether you are picking an option from a powder coating color chart or choosing a custom powder coating. It is also crucial to know the role of surface preparation in color perception, durability, and texture creation.
This guide explores the fundamental aspects of powder coating colors, including formulation, selection criteria, application techniques, and key industry standards.
Understanding Powder Coating Colors
Powder coating colors are categorized based on several factors, including finish, texture, and application-specific requirements. Solid colors are uniform, single-shade coatings that offer a clean, consistent appearance. Colors like back, white, red, blue, and yellow are commonly used in industrial, automotive, and architectural applications. Metallic powder coating colors create a shimmering effect, and silver, gold, and chrome-like finishes are often used in high-end consumer products, aerospace, or automotive industries.
Transparent or translucent colors allow underlying textures and base materials to be visible and are often used in decorative applications on furniture and signage. This effect can also be created or enhanced with controlled abrasive blasting techniques. RAL and ANSI standard colors like RAL 9005, Jet Black, and ANSI 61, as well as the gray used on electrical enclosures, ensure color consistency across projects and industries.
What Colors Does Powder Coating Come In?
There are many standard color options available for powder coating, but powder coaters can also try more unique powder coating colors based on their application. From color-changing powder coatings to eye-catching neon shades, you can choose from a variety of options:
- Fluorescent powder coating colors
- Metallic powder coating colors
- Neon powder coating colors
- Opalescent powder coating colors
- Pearlescent powder coating colors
- Translucent powder coating colors
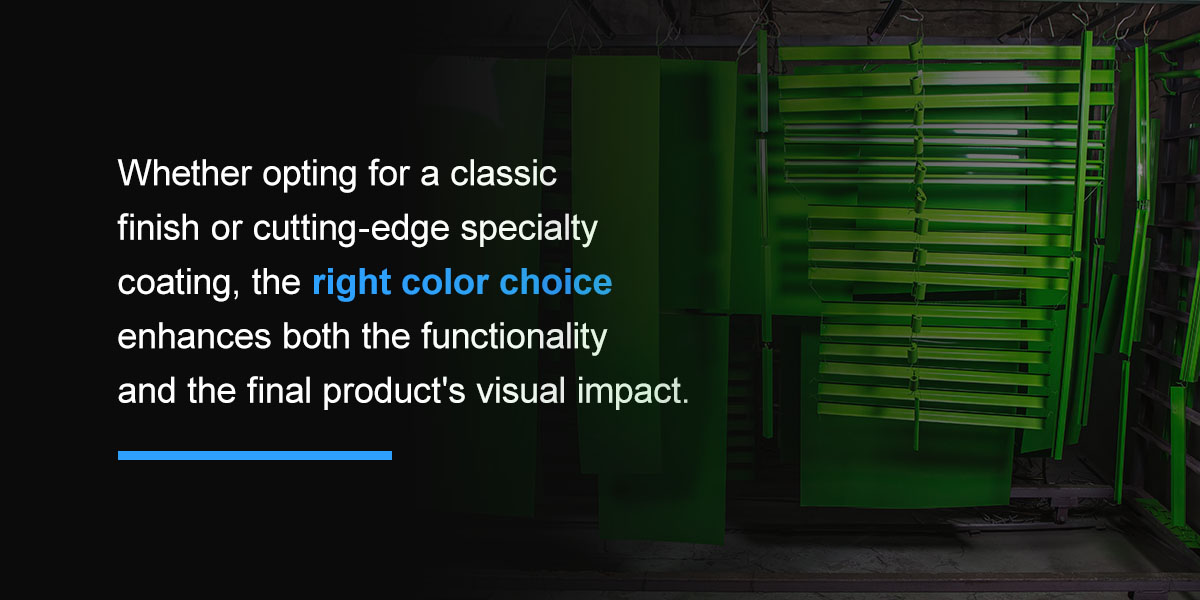
With custom formulations and advanced pigments, powder coating offers nearly unlimited design potential for the automotive, aerospace, architecture, and consumer goods industries. Whether opting for a classic finish or cutting-edge specialty coating, the right color choice enhances both the functionality and the final product’s visual impact.
Emotional Impact of Powder Coating Colors
Color psychology is crucial in product perception, branding, and user experience.
For example, red evokes feelings of energy, urgency, and excitement, which is why it is commonly used in safety applications. Blue represents professionalism and trust and is frequently used on industrial machinery and medical equipment. White conveys cleanliness and modernity and is present in laboratory equipment and appliances. Matte and satin finishes are also popular with electric vehicle manufacturers for their clean, futuristic appearance.
Green is associated with eco-friendliness and renewal, making it ideal for agricultural equipment. Yellow signals caution and high visibility, which is handy when applied to warning signs, construction machinery, and sporting goods. Gray suggests stability and is a preferred colorway for technology, military, and infrastructure applications.
The Science Behind Powder Coating Colors
Powder coatings consist of several key ingredients that influence their color, texture, and performance characteristics. The process involves precisely blending raw materials to deliver consistent color, durability, and adherence to specific industry requirements. Key components include:
- Resins: Epoxy, polyester, polyurethane, or acrylic resins determine the powder coating’s durability, adhesion, and chemical resistance. Resins serve as the primary binder.
- Curing agents: These react with resins to create a crosslinked, durable finish. Different curing agents are used for specific performance attributes, such as heat tolerance or impact resistance.
- Pigments: Pigments provide color and opacity, with pigment options including bright, vivid hues and inorganic, earthy, and muted tones.
- Fillers: Fillers are added to the substrate to enhance the powder coating’s mechanical properties, improve consistency, and modify surface texture.
- Additives: Additives control gloss levels, enhance ultraviolet (UV) stability, or introduce special effects. Examples include flow modifiers for a smooth finish, matting agents for gloss control, and anti-gassing agents for pinhole prevention.
Pigment Chemistry and Color Stability
The choice of pigments affects the color’s fade resistance, thermal stability, and chemical compatibility.
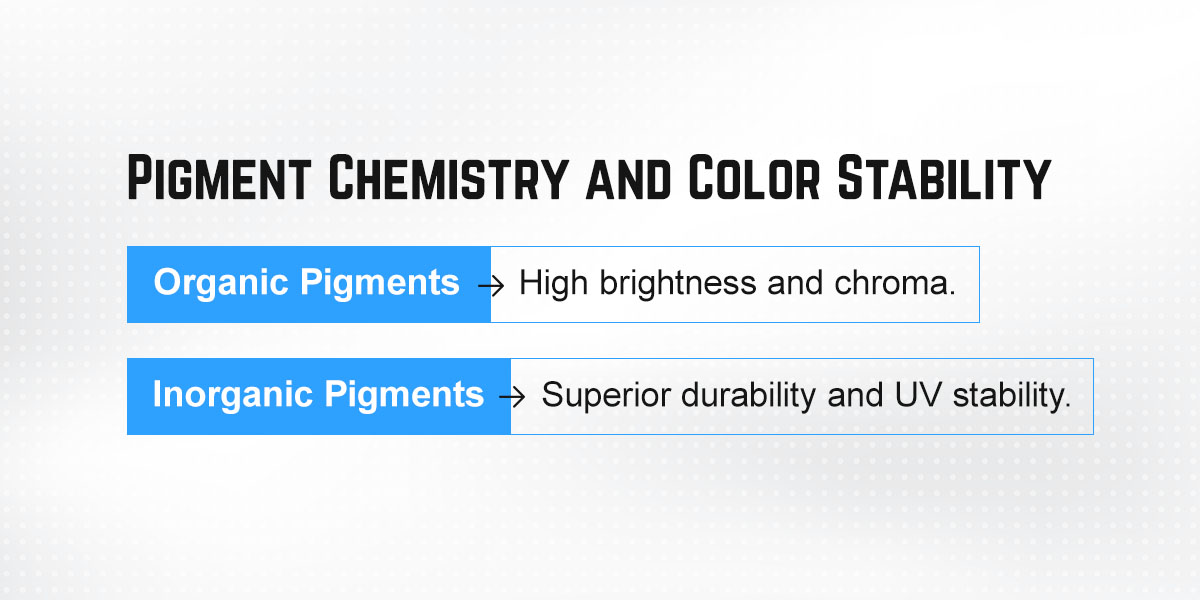
Organic pigments, such as azo, which is used in reds or yellows, and phthalocyanine, which is used to create blues or greens, provide high brightness and chroma but may have lower UV resistance.
Inorganic pigments offer superior durability and UV stability, making them appropriate for outdoor applications. Examples include iron oxides, which are reds and browns, chromium oxide, which is green, and titanium dioxide, which is white. Metallic and special effect pigments, usually aluminum or mica-based pigments, create reflective or textured color finishes that enhance the aesthetic appeal.
2 Types of Powder Coating Powders
Powder coatings are formulated to meet specific performance, durability, and environmental requirements across industries. They are categorized based on their resin chemistry, application conditions, and intended use. When reviewing a powder coat color chart, you’ll notice two distinct types.
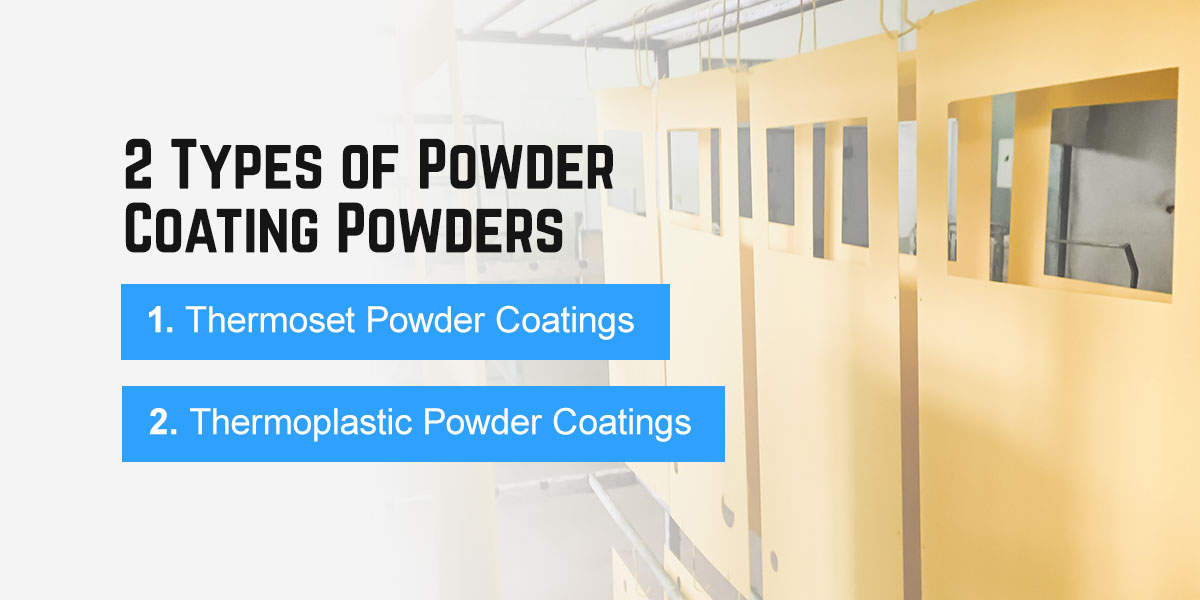
1. Thermoset Powder Coatings
When cured, thermoset powders undergo an irreversible chemical crosslinking reaction, forming a durable, heat-resistant finish. Options include:
- Epoxy powder coatings: These powder coatings have superior chemical resistance but are not UV-stable. They are best for use in automotive, marine, and industrial applications.
- Polyester powder coatings: Ideal for outdoor structures, architectural components, and consumer goods, polyester powder coatings are highly resistant to UV and weather and offer excellent flexibility.
- Epoxy-polyester powder coatings: This hybrid combination is used in general industrial applications for its durability and weather resistance.
- Polyurethane powder coatings: These powder coatings are used in agricultural equipment, automotive parts, and medical devices. They offer good abrasion, chemical, and weather resistance.
- Acrylic powder coatings: Used in automotive clear coats, this product provides a high-gloss, smooth finish with reliable color retention properties.
2. Thermoplastic Powder Coatings
Thermoplastics do not have a chemical reaction during curing. They can be remelted and reshaped, offering superior impact resistance and corrosion protection:
- Nylon powder coatings: These are resistant to wear, chemicals, and moisture, making them ideal for use in medical equipment, automotive components, and food-grade applications
- Polyvinyl chloride (PVC) powder coatings: Common in coated wire racks, tool handles, and marine components, PVC powder coatings offer high chemical resistance and flexibility.
- Polyolefin powder coatings: These coatings are highly chemical- and corrosion-resistant and are applied to pipelines, electrical enclosures, and automotive parts.
Choosing Powder Coating Colors
Color selection is both an aesthetic and functional decision, influenced by industry standards, market trends, and material performance considerations. As technology advances, more innovation in color effects, environmental sustainability, and customization is to be expected. To ensure consistency and repeatability, the powder coating industry follows standardized color-matching systems, including:
- RAL color system: This is a European standard widely used for industrial applications. It provides a catalog of over 200 colors with standardized formulations.
- Pantone matching system (PMS): More commonly used in branding and graphic design, PMS can be converted into powder coating equivalents.
- Federal Standard 595: Used in military and government applications, Federal Standard 595 provides a structured numbering system for approved colors.
Factors Influencing Color Choice
When selecting a powder coating color, first consider the environmental exposure of the material being coated. UV, humidity, and chemical exposure can dictate pigment selection and resin type. The substrate material, whether steel, aluminum, or another composite, will interact differently with various types of powders, affecting the final color appearance.
Similarly, matte, satin, and high-gloss finishes influence color depth and brightness. The chosen application method, whether electrostatic spray or fluidized bed, also impacts coating thickness and opacity.
Color consistency is critical in industries where uniform appearance, branding, and product quality are essential. Variations in shade, gloss, or texture can result in rework, product rejection, or customer dissatisfaction.
Powder Coat Color Matching
Manufacturers offer custom powder blends tailored to specific branding or design requirements. This customization involves a spectrophotometer analysis, which ensures precise color formulation.
The instrument directs light onto the powder-coated sample and records the reflected wavelengths. Then, the instrument quantifies the color in numerical values based on standard color spaces like RGB or CIELAB. Manufacturers use this method to detect deviations in color formulation, ensuring uniformity across production batches. Batch-to-batch consistency testing guarantees minimal variation, or prototype sampling verifies the final appearance before full-scale production.
Stock powders are more cost-effective and readily available. Custom formulations require additional lead time and often have costly minimum order quantities. Small-batch custom coatings are usually available from specialty providers, which offer rapid prototyping with minimal order requirements.
Finishing and Special Effects
Can powder coating be different colors and finishes? Powder coating colors are available in a variety of effects, each suited to different aesthetic and functional requirements. Common finish types include gloss levels and surface effects, including textured powder coating colors.
High gloss is vibrant and easy to clean, semi-gloss balances aesthetics with durability, and matte reduces glare, enhancing subtle color tones. Smooth surfaces leave a uniform appearance with minimal texture. Wrinkle effects add a rough, textured feel for grip-enhanced surfaces, and hammertone creates an industrial-style, dimpled texture that hides imperfections.
Special effects finishes include:
- Metallic: Metallic powder coating colors use aluminum flakes or pearlescent pigments for a shimmering effect.
- Candy colors: Candy colors are created by using a transparent topcoat over a metallic base to create a deep, rich finish.
- River and vein: River and vein textures mimic natural stone or anodized finish and are commonly used in decorative applications.
- Tinted coatings: Tinted coatings protect based colors while modifying hue or gloss.
Powder Coating Application Techniques
Powder coating is applied in one of three ways. The most common method is electrostatic spray disposition (ESD), where the powder is charged and adheres to a grounded metal surface. For thicker coatings, fluidized bed dipping is used, which ensures high-durability applications. Tribostatic application uses friction charging for improved adhesion on complex geometries.
Maintaining consistent color across production batches, whichever application method is used, requires:
- Controlled curing conditions: Temperature fluctuations can alter gloss and hue. Thermal curing in an oven triggers crosslinking and hardens the coating. Infrared and UV curing is used for heat-sensitive materials, accelerating processing times.
- Proper powder storage: Humidity and contamination affect powder flow and final appearance.
- Equipment calibration: Ensuring uniform electrostatic charging prevents uneven application.
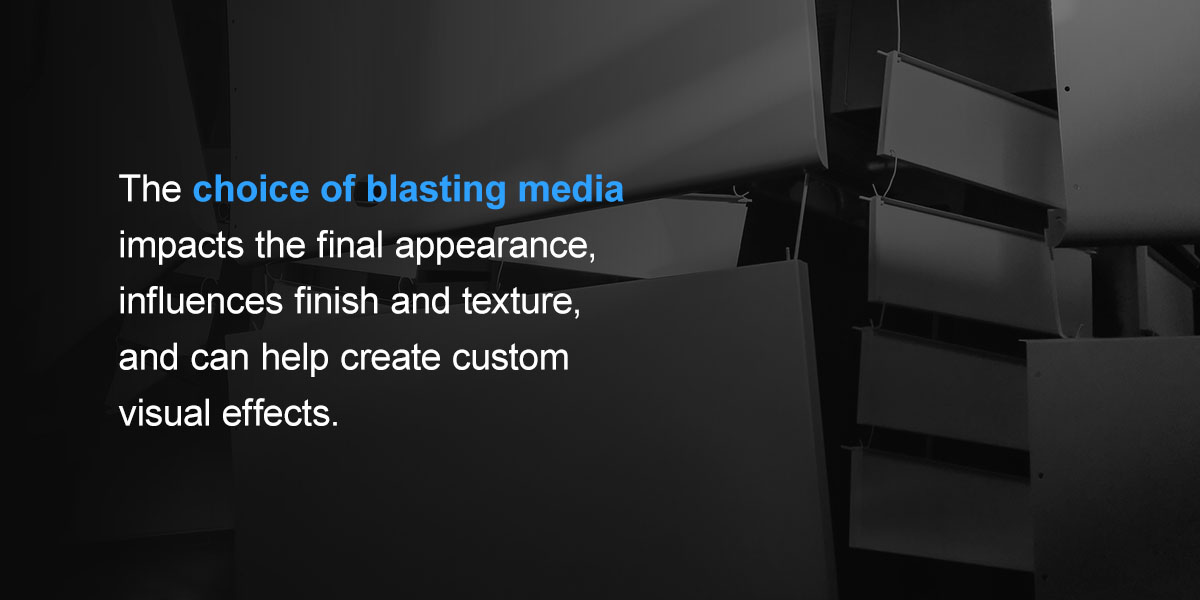
The impact of these pigments relies on their manufacturing quality as much as surface preparation on the final product to deliver long-lasting, high-quality finishes. The choice of blasting media impacts the final appearance, influences finish and texture, and can help create custom visual effects. Different abrasive blasting techniques can influence how the pigments interact with light, which is especially relevant for specialty finishes.
Advantages and Challenges of Powder Coating
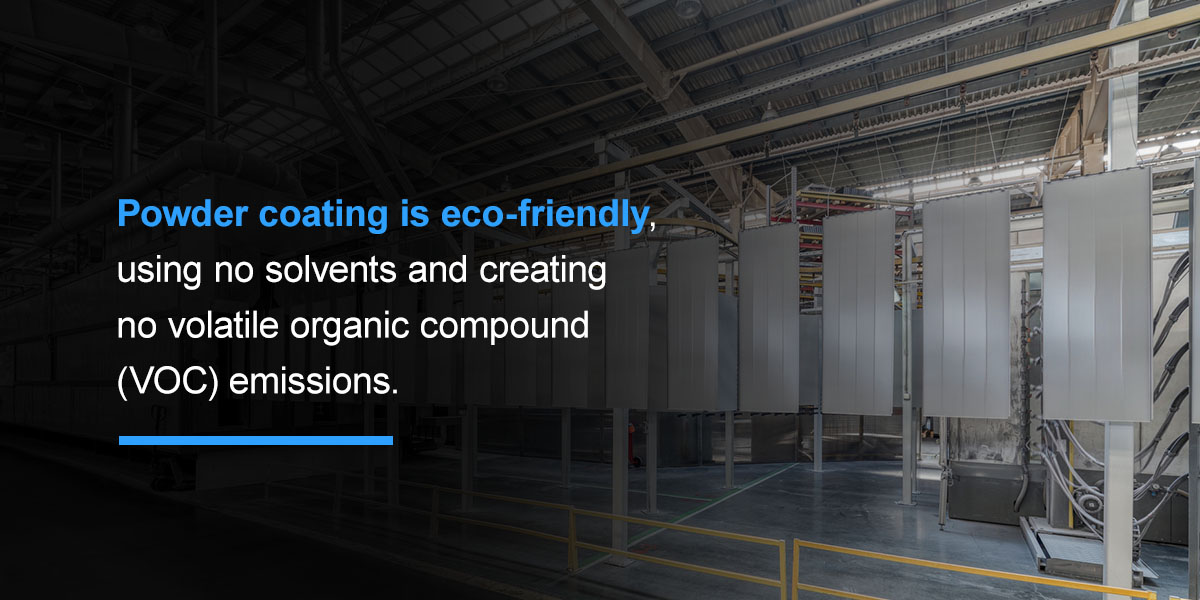
There are various benefits to using powder coating. It is durable, offering resistance to corrosion, chemicals, and impact. It is also eco-friendly, using no solvents and creating no volatile organic compound (VOC) emissions. This application method also provides even coverage with various textures and gloss levels.
However, contaminants or oxidation can lead to poor adhesion. High curing temperatures can also restrict the use of heat-sensitive substrates. To achieve optimal adhesion, surfaces must be properly prepared before powder coating. Abrasive media blasting is critical in removing coatings, corrosion, or other unwanted surface residues.
Regulatory Considerations and Color Standards
Original equipment manufacturer specifications dictate approved colors, gloss levels, and durability requirements for powder coating in the automotive and aerospace industries. Many manufacturers adhere to RAL and Pantone color systems.
In architecture and construction, colors must align with building codes, energy efficiency ratings, or aesthetic requirements. Reflective coatings in light grays, silvers, and whites are common for energy conservation. Regulatory standards often require coatings in medical and food-grade applications to be non-toxic, easy to clean, and resistant to microbial growth.
Environmental and Safety Considerations
Adherence to color standards, regulatory compliance, VOC limits, and environmental considerations is critical to ensuring product quality, industry acceptance, and sustainability. Understanding these factors helps manufacturers maintain consistency, meet safety requirements, and enhance the long-term performance of coated products. Key regulatory requirements are:
- VOC limits: VOCs contribute to air pollution and health hazards. As powder coatings contain little to no solvents, they are compliant with EPA, EU REACH, and California Air Resources Board regulations.
- Occupational Safety and Health Administration (OSHA): Employers must comply with OSHA’s permissible exposure limits for powder coating components like curing agents and metallic pigments.
- European Union REACH: The chemical substances used in powder coatings should not pose environmental or human health risks. The European Union REACH places restrictions on heavy chemicals like lead chromates and hazardous substances in pigments.
- ISO 14001: ISO 14001 for environmental management systems certifies that a manufacturing facility adheres to environmental best practices that reduce pollution and resource consumption.
Certifications That Boost Credibility
Obtaining industry-recognized certifications for products enhances brand reputation, customer trust, and regulatory approval. The following certifications demonstrate a commitment to quality, environmental responsibility, and consistency in powder coating:
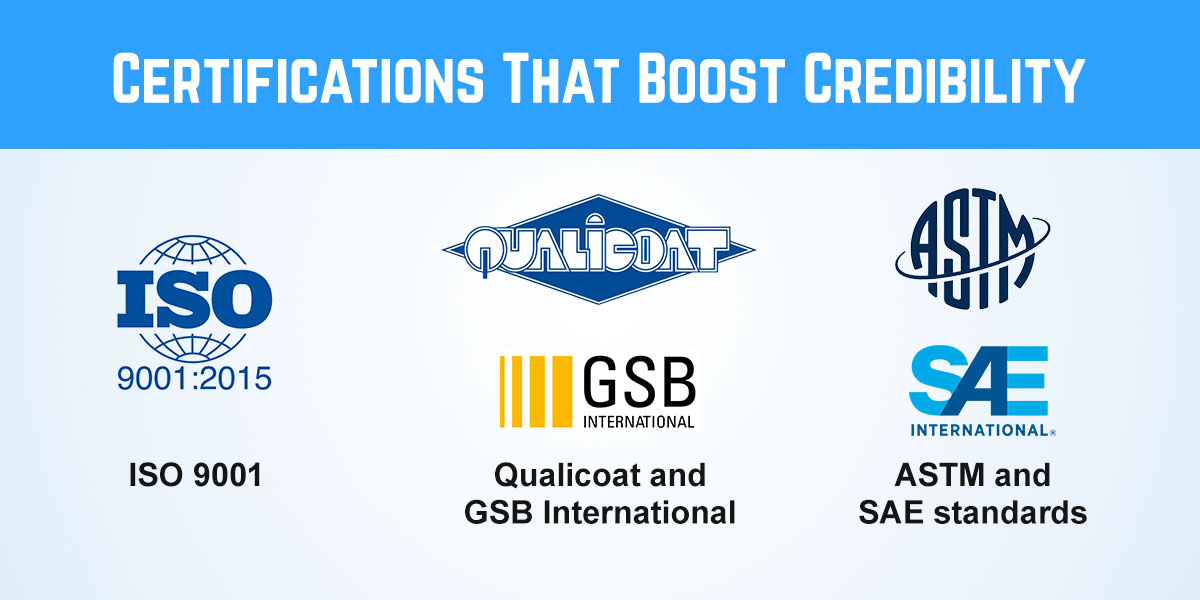
- ISO 9001: The certification for quality management systems ensures consistent color quality, adhesion, and durability through standardized manufacturing processes.
- Qualicoat and GSB International: The European certifications for high-performance aluminum coatings in architectural applications ensure compliance with adhesion, weathering performance, and coating thickness.
- ASTM and SAE standards: ASTM D3359 tests the adhesion strength of powder coatings, while SAE J2527 evaluates weathering resistance in automotive coatings.
The Power of Sandblasting
Sandblasting creates a clean, uniform surface, improving powder coating performance and longevity. Sandblasting helps remove old or failed coatings, leaving a clean, uniform surface for refurbishing or recoating metal parts. It also eliminates oxidation and corrosion by removing rust and mill scale to prevent premature coating failure.
Apart from removal, sandblasting also aids in surface preparation. The process creates a roughened surface for stronger powder coating adhesion, which is especially useful in preparing difficult-to-cut materials like aluminum, stainless steel, and other non-ferrous metals. Proper preparation minimizes defects to ensure coatings adhere effectively and maintain their protective properties over time.
Powder Coating with Superoxalloy
Superoxalloy is a high-performance abrasive media engineered for efficient surface cleaning and preparation. It is composed of advanced oxide-based compounds, providing superior abrasion, durability, and efficiency compared to traditional blasting materials like garnet, steel grit, or aluminum oxide.
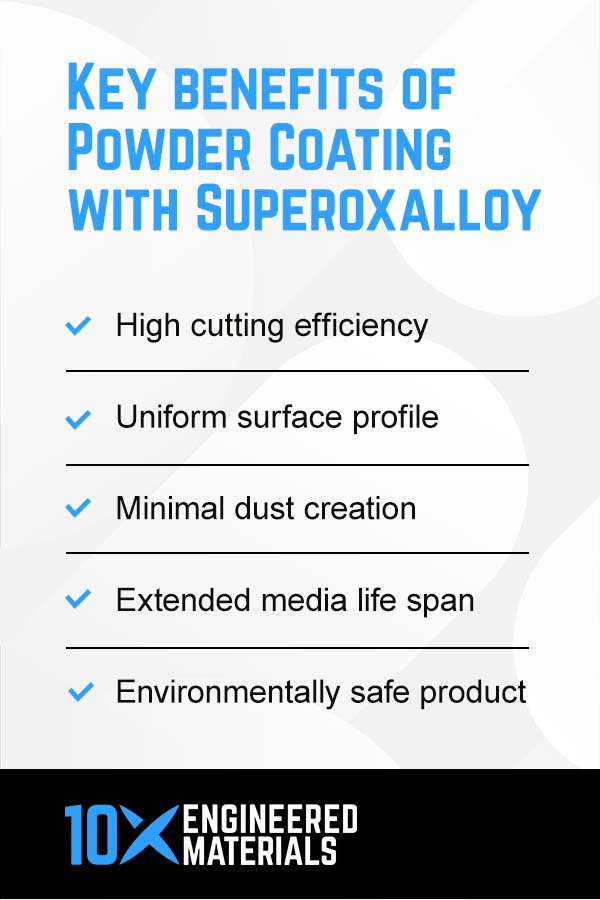
This product improves the surface profile and offers better economics than legacy abrasives in terms of productive output, safety, and cost-efficiency. Key benefits extend to:
- High cutting efficiency: This product removes coatings and contaminants quickly with minimal material waste.
- Uniform surface profile: Superoxalloy creates an optimal surface profile for powder coating adhesion, thanks to its patented mix of shapes.
- Minimal dust creation: Unlike traditional sandblasting materials, superoxalloy reduces airborne dust during blasting operations, improving workplace safety and visibility.
- Extended media life span: It outlasts conventional abrasives and can be reused in future projects, lowering operating costs.
- Environmentally safe product: Superoxalloy products are inert. It is the only abrasive on the market that is biosoluble in human lungs, ranking in the same category as coffee for safety.
EpiX Superoxalloy Abrasive
EpiX is available in EpiX LP for low profile and softer metals and EpiX MP for powder coating, paint, corrosion, liquid coatings, and applications requiring an SP-5 white metal finish. It is also available in EpiX EP, which makes quick work of extra hard coatings, including mill scale removal. It offers precise removal, with no burn-off or scraping necessary, delivering a ready-to-coat surface in quick succession.
Successfully Remove Powder Coating With Superoxalloy Abrasives
Powder coating comes in many colors and finishes, combining durability, sustainability, and aesthetic versatility. From RAL and Pantone-matched shades to custom metallic, textured, and specialty finishes, the possibilities for achieving durability, corrosion resistance, and design precision are virtually limitless. As industries demand higher durability and precision, using advanced blasting media provides a competitive advantage to manufacturers, as well as industrial maintenance and high-performance coating applications.
10X Engineered Materials manufactures and supplies premium-quality abrasives for a wide range of industrial applications. Our custom-engineered superoxalloys allow you to optimize your blasting systems for any project. These products are made from a mineral wool by-product, making them the safest blasting abrasives on the market.
Explore our EpiX line today to get the most technologically advanced blasting media.