Visibility is crucial to efficient and effective sandblasting operations. Taking steps to create a cleaner work environment within the blast cabinet can help your team optimize operations and deliver high-quality results. Explore how to improve blast cabinet visibility in three easy steps below.
Understanding Blast Cabinet Dust
Dust generated during sandblasting processes directly impacts worker visibility and productivity. Understanding what causes higher amounts of dust and common misconceptions about managing excess debris is the first step in improving blast cabinet operations.
Dust Sources and Their Impact on Operations
Several factors impact dust generation during sandblasting. The abrasive media used can break down upon impact. The media can pulverize paint, rust, or elastomeric coatings present on the substrate material or the substrate itself. All these elements can contribute to small particles floating around in the cabinet during blast cabinet operations.
Abrasive metering is one of the most important considerations for controlling dust levels. Operators can control the abrasive media flow and how much material combines with the compressed air stream — this directly influences sandblasting strength and dust generation. In suction and pressure cabinets, abrasive overfeeding is the leading cause of increased dust during sandblasting.
Visibility becomes more challenging as dust accumulates in the blast cabinet, impacting overall performance.
Dust Management
Effective dust management is key to better sandblasting visibility. A common misconception is that higher airflow within the blast cabinet is the only way to create a cleaner, more efficient working environment. However, the abrasive media you use can be just as important to reducing dust generation as adjusting the airflow.
3 Steps for Enhancing Blast Cabinet Visibility
A few quick steps will help you maintain better visibility during sandblasting operations.
Step 1: Ensure Proper Metering
Proper metering will significantly improve visibility. Consider the following:
- Metering valve type: The right, high-quality valve will offer precise control and more consistent flow. Always choose a metering valve designed for the abrasive material you are working with.
- Tuning techniques: Adjust your metering valve setting in small increments to fine-tune your mixture of air and abrasive material. Record the optimal setting for future reference.
- Lighting: An adequate lighting solution will support visibility by minimizing shadows or glares while illuminating the work area.
Another important consideration is your dust collection system size. Ensure it is properly suited to your cabinet. If you are not using a dust collector, the abrasive media you work with is even more crucial. The media is hyper-critical to managing dust. Grit replacement schedules should be compressed to combat excess dust.
Step 2: Use Effective Dust Control Techniques
Routine maintenance is crucial for any low-dust solutions for cabinet blasting. If you work with dust collection systems, your filters will impact performance and visibility. Explore a few tips for maintaining proper blasting conditions below:
- Ensure filters are pulsed and cleaned prior to the working session.
- Replace the air filters if the airflow is still insufficient after cleaning.
- Replace the filters if your dust collector’s pressure drop gauge can no longer drop to 2 inches of water column.
If you continue experiencing overfeeding after adjusting the metering valve, inspect its condition. The internal components do wear over time, which impacts overall performance. Replace these as needed to support better blasting conditions.
Proper metering and air supply settings are key to optimizing your blast experience. If your abrasive is underfed, the blasting process will be inefficient. When your abrasive is overfed, you will likely experience excessive dust and abrasive consumption, making visibility more challenging as you work.
Step 3: Switch to Superoxalloy Abrasives
The next step in addressing a dusty blast cabinet is switching from old abrasives, such as silica sand or mineral slags, that break down quickly and negatively impact visibility. Upgrading to superoxalloy abrasives is the best way to reduce dust generation. This option is a high-performance blasting media consisting of an engineered alloy of oxide minerals. It is known for its durability, versatility, and unmatched safety.
Superoxalloy abrasives break down more slowly than other common media, resulting in low dust accumulation during blasting operations. They also tend to be more cost-effective than alternatives, thanks to their longer lifespan, reclaimability, and performance.
At 10X Engineered Materials, we offer various superoxalloy abrasives, including:
- EpiX: This super-precise option is best for precision manufacturing applications.
- KinetiX: KinetiX is a cost-efficient abrasive for high-production grades, and is suitable for commercial sandblasting.
- DynamiX: This abrasive is suitable for heavy-duty grades and tougher blasting applications, like rail car, ship hull blasting, or pipeline maintenance.
Our team can help you find the right options and profiles for your specific applications, supporting less dust generation and improved efficiency.
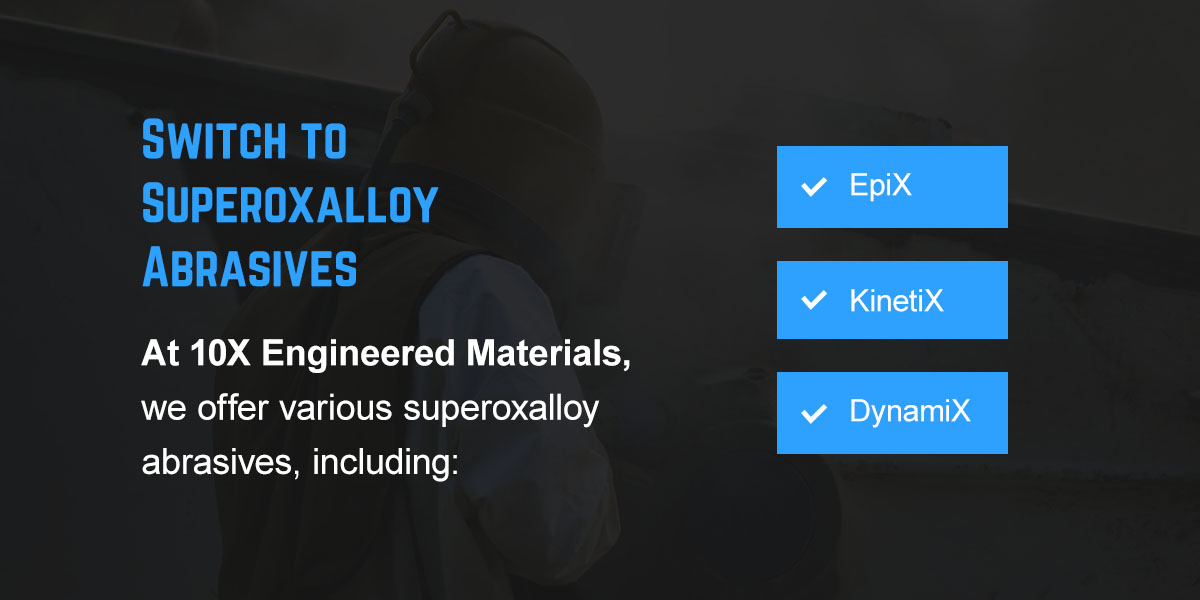
Benefits of Superoxalloy Abrasives
Superoxalloy abrasives are the leading choice for sandblasting operations. They offer several key benefits, making them the ultimate media for nearly any application. In addition to providing a low-dust working environment for your team, below are key advantages of choosing these abrasives for your next job.
Performance
When you need a media that offers high-quality finishes while creating minimal surface damage, superoxalloy abrasives are the best option because of their strong, amorphous structure. Their particles do not easily shatter on impact, helping to reduce dust and particle embedment on the substrate material.
A key benefit of working with these abrasives is creating a surface that is ready for further processing immediately after blasting.
Cleanliness
Maintaining a clean working environment in the blast cabinet is easier with low-dust options, like superoxalloy abrasives. Greater visibility enables greater precision and higher efficiency during blasting applications, supporting improved outcomes.
Safety
Another key reason to switch to superoxalloy is its safety. This media has a clean health and safety profile. The superoxalloy abrasives from 10X Engineered Materials are the most safety-tested abrasive material and the only biosoluble abrasive material on the market.
Sustainability
Superoxalloy abrasives are a more environmentally friendly choice than other blasting media because they generate low amounts of dust and reduce waste. The material is also less dangerous than traditional abrasives like silica sand, eliminating the risk of potential contamination. Your team can enjoy sandblasting operations that are better for them and the planet.
Experience Breakthrough Sandblasting Performance With 10X Engineered Materials
When you need high-performance blasting products, turn to 10X Engineered Materials. We offer a selection of safe, environmentally friendly, and innovative superoxalloy abrasives to enhance your sandblasting applications, which are low-dust solutions for cabinet blasting.
We prioritize cost-effectiveness and quality so you can embrace improved blasting processes while saving money. Our team can help you find the right products for your specific needs from our family of abrasives.
Contact us to learn more about the superoxalloy abrasives from 10X Engineered Materials, or find a local distributor to get started.
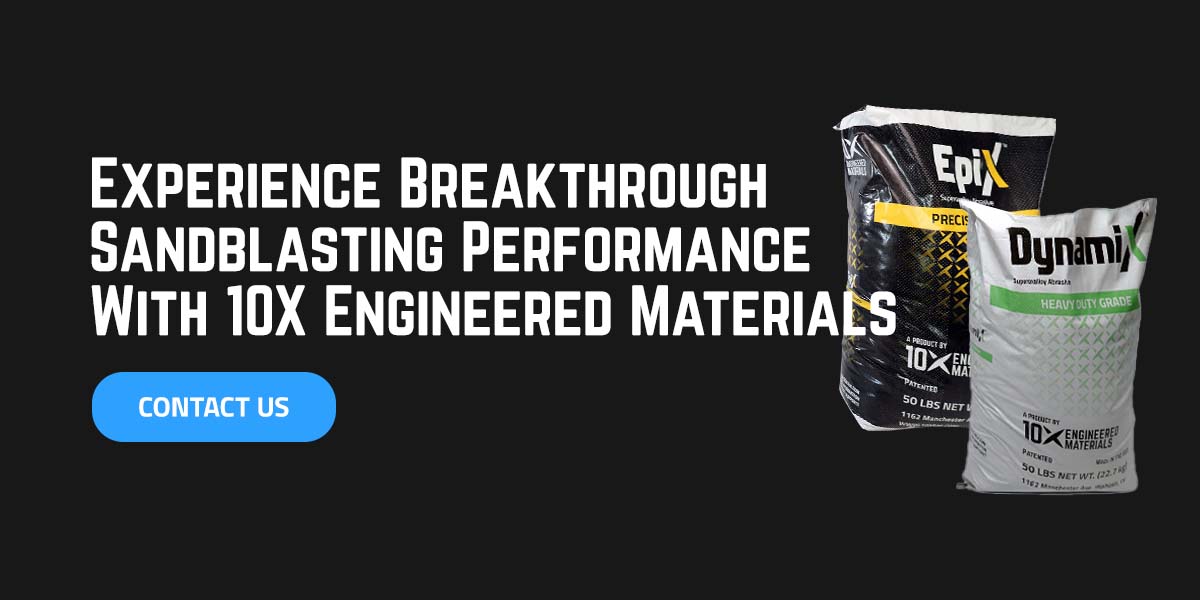