Sandblasting is a precision-driven process that relies on high-velocity abrasive media to remove corrosion, coatings and surface contaminants. The choice of abrasive directly affects the longevity and efficiency of blasting equipment. Worn-out sandblasting equipment impacts your organization’s productivity, reliability and overhead, making it essential to mitigate the risks of unplanned maintenance and parts replacement.
Understanding abrasive properties like hardness, density, shape and composition can help you mitigate excessive wear on machinery, reduce downtime and optimize operational costs.
The Mechanics of Abrasives and Equipment Interaction
Blasting equipment, including nozzles, hoses, metering valves, pressure valves and reclaim systems, is subject to constant wear from abrasive particle impact. The degree of wear depends on several key abrasive properties:
- Hardness: Harder abrasives, such as silicon carbide and aluminum oxide, provide aggressive cutting action but accelerate wear on blast nozzles, hoses and valves.
- Shape: Angular abrasives, like crushed glass and garnet, can cause high stress concentrations and uneven wear.
- Density: Denser abrasives, like steel grit or chilled iron, generate higher stress forces within a blasting system, which leads to increased wear on consumable parts and reclaim systems.
- Composition: Chemically reactive abrasives like sodium bicarbonate can introduce corrosion risks, while silica-based media generate fine dust that embeds itself into seals and bearings.
Operators must balance efficiency with equipment longevity by selecting abrasives with an optimal hardness-to-wear ratio. The Mohs hardness scale is a key metric in selecting abrasives, as a mismatch between media and equipment metallurgy leads to premature failures.
Erosive Wear
Abrasive media wear on equipment is commonly seen in the form or material erosion. Erosive wear results from high-velocity particle impact that gradually removes material from equipment surfaces. This effect is prevalent in blast nozzles, where the highest-velocity abrasives erode the orifice and venturi, altering spray patterns and reducing efficiency. It is also visible in reclaim system ducting, where fine particles abrade the interior surfaces, leading to leaks and reduced dust collection efficiency.
Impact Wear
When heavy abrasives high in kinetic energy strike a surface, they cause impact wear through deformation and material loss. It is most common inside pressure vessels, where metallic abrasives can cause localized fatigue damage, as well as in the impellers in wheel blast systems, causing material embrittlement and failure.
Sliding Wear
Abrasive particles moving across surfaces under pressure can cause sliding wear. This is especially common with abrasives like crushed glass. Hoses and metering valves are particularly vulnerable, as continuous abrasive flow can gradually wear down the material, increasing the risk of rupture. Blast cabinets are also susceptible, where media reclaiming and reflow create persistent frictional wear.
Corrosive Wear
Certain abrasives introduce chemical reactions that degrade equipment surfaces over time. Steel components exposed to moisture-retaining abrasives can accelerate corrosion formation. Seals and gaskets are also prone to corrosive wear, where chemical interaction with fine dust particles causes premature failure.
Fatigue Wear
Repeated stress cycles due to abrasive impact can lead to microcracks and structural failure in pressure vessels, where high-density media increases cycle loading. The continuous abrasive flow in hopper walls can also generate stress fractures.
Cost Implications of Sandblasting Equipment Wear and Tear
The continuous degradation of hoses, nozzles, metering valves, pressure vessels, and reclaim systems directly impacts operational expenses, direct equipment costs, downtime, and overall efficiency.
Productivity halts when a critical component like a nozzle or hose fails mid-operation. The cost of labor and lost blasting time adds up, especially in high-volume industrial settings. A worn nozzle can also result in an irregular blast pattern, reducing effectiveness and requiring additional passes to achieve surface specifications. These factors increase labor costs and media consumption.
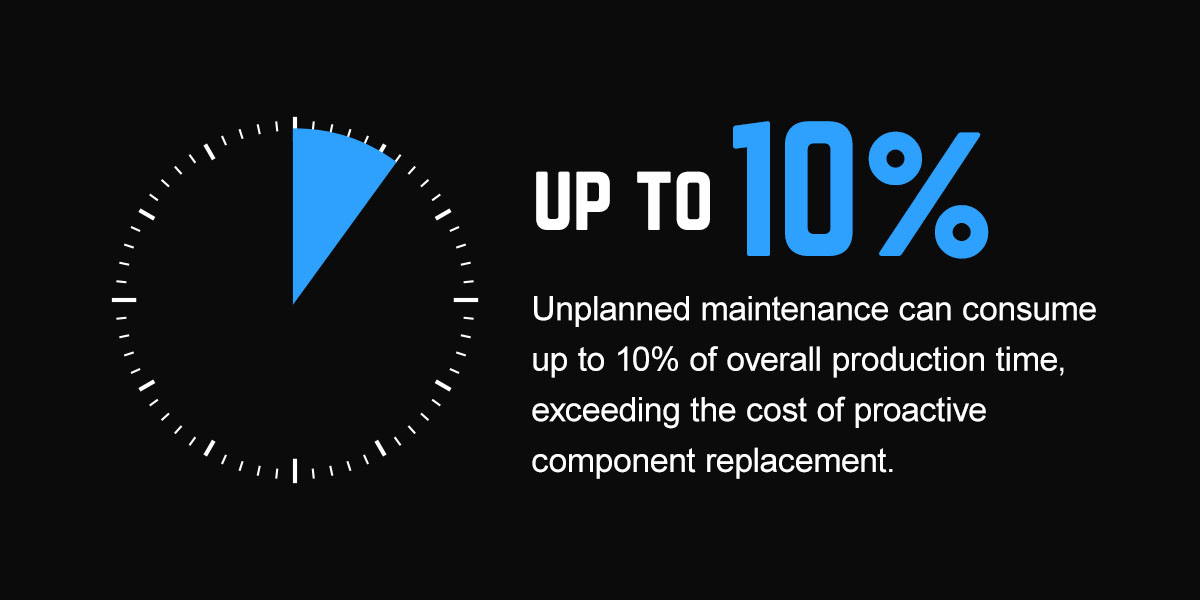
Over months and years, these incremental costs compound into substantial financial burdens. These include annual equipment replacements and cumulative downtime costs. Unplanned maintenance can consume up to 10% of overall production time, exceeding the cost of proactive component replacement.
How to Mitigate Abrasive Wear
Operators should select abrasives with low reactivity relative to their equipment materials to mitigate chemical wear. Additionally, rigorous moisture control in blast media storage can prevent corrosion-related failures in abrasive and blasting systems. Best practices for extending equipment life include:
- Optimize abrasive selection: Match hardness, shape, and density to your equipment’s specifications to reduce unnecessary wear.
- Invest in durable components: Use tungsten carbide or boron carbide nozzles for high-wear applications.
- Replace parts regularly: Track nozzle orifice size and valve integrity and reclaim system condition to mitigate abrasive wear on equipment.
- Implement proper media filtration: Prevent contamination that can accelerate equipment degradation.
- Maintain correct air pressure: Overpressurization increases impact velocity and equipment strain.
Superoxalloy Products Are the Solution
Superoxalloy products are wear-resistant abrasive materials that combat the extreme conditions of sandblasting applications. With superior hardness and high corrosion resistance, this product significantly extends component life, reduces downtime, and optimizes system performance. The alloy’s unique structure not only distributes stress more effectively, but it is much more efficient, so you need a lot less abrasive per unit area blasted, reducing localized wear on sandblasting equipment and high-impact components like nozzles, metering valves, and reclaim system parts.
The oxidation-resistant formulation of superoxalloy helps prevent chemical reactions which accelerate corrosion. The use of superoxalloy can help to ensure the long-term durability of your blasting equipment in harsh operating conditions. Thanks to the product’s reusability, these features work together to extend equipment life by up to 25% and decrease abrasive consumption by up to 80% per square foot.
Cost-Saving Advantages
The cost benefits of switching to superoxalloy products far outweigh potentially higher initial investment costs:
- Less need for replacements: Extended service life reduces the frequency of part replacements, significantly lowering material expenses over time.
- Improve energy efficiency: Consistent nozzle performance lowers compressed air consumption, which can decrease energy costs.
- Reduce downtime: With fewer maintenance interventions, operators can maintain higher productivity levels, generating more revenue.
- Optimize abrasive consumption: Maintaining nozzle and metering valve integrity ensures proper media flow, preventing excess abrasive use and reducing operational waste.
Partner With 10X Engineered Materials Today
Abrasive wear is not just an operational inconvenience. It is a significant financial liability. Without proper management, small inefficiencies in equipment wear lead to escalating costs in replacements, downtime, media waste, and energy consumption. By strategically selecting abrasives, investing in durable components, and optimizing blasting parameters, sandblasting professionals can dramatically reduce long-term expenses while maintaining high-efficiency operations.
At 10X Engineered Materials, we continuously innovate sustainable blasting technologies. Switching to EpiX, KinetiX, or DynamiX abrasive media can improve worker safety, reduce your organization’s environmental impact, and contribute to long-term cost savings. We offer on-site demos, personalized consultations, and ongoing technical support to ensure you see optimal results.
Contact us today to discuss your requirements for abrasive blasting.