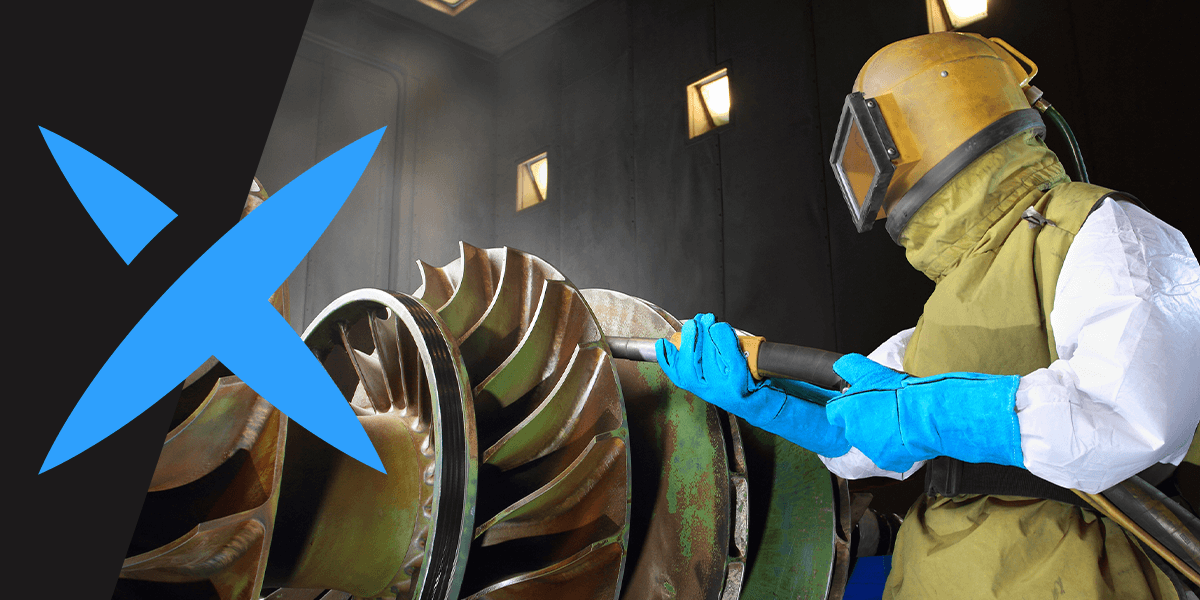
Sandblasting, or abrasive blasting, requires high-pressure equipment to blast abrasive media particles onto a surface or substrate. Businesses across industries use abrasive media blasting for applications such as surface preparation, corrosion removal, rust removal, equipment cleaning, descaling, coating removal, and even brick restoration.
While abrasive blasting yields many benefits, you must understand the potential dangers and risks before the start of your project. Our guide will explore what is bad about sandblasting to ensure you are more protected on the jobsite.
5 Sandblasting Hazards
From crystalline silica to slag and walnut shells, aluminum oxide, glass beads, garnet, crushed glass, steel grit, stainless steel grit, steel shot, and stainless steel shot, businesses can use various abrasive blasting media for their projects. The various media also differ in their degree of risk. Consider some of the most common sandblasting health hazards when making your media selection:
1. Respiratory Dangers
A common sandblasting respiratory hazard is respirable abrasive media dust. As most media shatters during the blasting process, workers face exposure to particles under 10 microns in diameter, otherwise known as respirable dust. These microscopic particles are easily inhaled and often without workers realizing it, and most abrasives are be bio-persistent, leading to health concerns such as increased risk of lung cancer, silicosis and chronic bronchitis.
The surface you are preparing may also contain toxic materials, further contributing to sandblasting dust hazards. Workers need to protect themselves against these issues by using personal protective equipment (PPE). According to the Occupational Safety and Health Administration, employers are responsible for sourcing and paying for PPE in most cases.
2. Skin and Eye Issues
The blasting process requires air or water pressure to transfer abrasive blasting media onto a surface. Since media such as sand, garnet, or copper slag will impact the surface at high rates of speed, they have the potential to ricochet and injure bystanders. Some common injuries include:
- Skin abrasions: Abrasive media has an irregular shape, and these jagged edges can cause small cuts on workers’ skin. These wounds can become infected without proper treatment.
- Cornea irritation: Airborne particles may collide with workers’ eyes, resulting in redness and pain, or even more severe eye damage.
Employers can reduce the chance of skin and eye hazards by wearing appropriate PPE, such as blasting hoods, safety goggles, gloves, and protective overalls.
3. Noise Hazards
One of the more significant sandblasting dangers is hearing loss. The combination of workers operating high pressure air, the impact and the reverberation of the abrasives particles connecting with a surface makes blasting worksites loud environments.
Exposure to noises above 85 dB-weighted average decibels for extended periods can lead to long-term hearing loss. In addition, loud sounds can cause auditory conditions such as tinnitus. PPE, such as earplugs and blasting helmets, helps lower the risk of noise-related health issues.
4. Ergonomic Challenges
Operating a high-pressure blasting nozzle can lead to back and other physical injuries, especially if workers do not use proper alignment and movement processes. Workers must receive training on proper lifting techniques, such as:
- Preparation: Evaluate how many people are needed for the task and whether you need any equipment.
- Lifting: Assume a squatting position to pick up new loads. Once you have secured the object, straighten your legs and keep your back straight or slightly arched, and lift with your legs, not your back muscles.
- Carrying: When carrying an object, hold the load as close to your body as possible. Take small steps forward and avoid twisting your body.
- Setting down: Once you reach the destination, squat down and activate your core muscles. If necessary, bend your knees to set the object on the ground; again, avoid using your back muscles.
5. Environmental Impacts
The many types of abrasive media have varying environmental impacts. Here is a brief outline of the effects of the most common media:
- Garnet and silica sand: Garnet and silica sand are obtained through mining, and certain extraction processes can lead to water and air pollution. Additionally, clearing land for mining operations can negatively impact animal habitats.
- Slag: Coal, copper, and nickel slag can contain leachable heavy metals. Ineffective cleaning after a project can lead to these metals leaching into soil, air, and water.
- Steel shot or steel grit: While these abrasive media are relatively effective, they require excessive energy and carbon emissions to produce, leading to excess air pollution from the production process.
Safety Measures and Best Practices
While there is no denying the impact of sandblasting hazards, there are various practices companies can employ to keep their workers safe. Some methods include:
- Wearing proper PPE: Sandblasting is dangerous without appropriate safety gear or PPE. Items that offer workers significant protection include goggles, blast hoods, helmets, ear plugs, and protective gloves. Companies should ensure all employers engaging in sandblasting wear proper, well-fitting PPE whenever working.
- Prioritizing ventilation: Exhaust ventilation and dust collection systems help to capture or appropriately manage dust, reducing the quantity workers breathe in or the inability to see what they are working on. Installing these systems on-site helps to ensure the safety of workers and the neighbors, too.
- Using containment tools: Barriers such as curtain walls or fully enclosed and sealed containment systems help reduce the dust in the working environment during sandblasting. Specifically, using blast rooms or blast cabinets for smaller operations limits exposure to other workers.
- Avoiding windy conditions: Strong gusts of winds can accentuate the spread of dust and cause further hazards. Site managers should understand weather conditions and delay projects as needed to protect workers and the surrounding area.
- Training workers: Advising workers that it is unsafe to eat or drink while using abrasive media helps to reduce potential health risks. Workers should also remove and wash their PPE correctly after applications. Make sure all employees working with sandblasting media are fully trained and educated on how to do so properly. Special techniques, training, and certiciation can be required on heavy metal or lead removal jobs. For example, most lead removal jobs will require changing tents with HEPA filters and vacuums.
Using a Safer Abrasive
While employing best practices and industry-standard PPE helps you achieve a safer work environment, the most effective way to maximize your workforce’s health is to replace your current abrasive with the worlds safest abrasive blasting media. 10X superoxalloy fulfills this requirement, as the amorphous particles are resistant to fracturing, and the dust is biosoluble. In other words, less dust is created during blasting with superoxalloy abrasives, and the dust from 10X is harmless. In addition, this media holds the following safety certifications:
- Approved by the California Air Resources Board.
- Compliant with the Environmental Protection Agency based on the Toxicity Characteristic Leaching Protocol test.
- Passed Washington state environmental testing specification, publication #80-12.
- The World Health Organization’s International Agency for Research on Cancer (IARC) conducted a comprehensive review of the massive body of studies on mineral wool material in 2002. After analyzing over fifty years of gold-standard human, animal, and laboratory toxicological studies, the IARC panel of experts unanimously concluded in their 2002 Monograph (Volume 81) that:
- Lack of evidence of excess illness or mortality in decades of human epidemiological studies following 26,000 exposed workers in the U.S. and Europe starting in the 1930s.
- Lack of evidence of lung damage, cancer, or decreased lifespan in multiple species of animals repeatedly exposed to high respirable dust concentrations over 80% of their lives (rats were exposed to dust for 6 hours per day, 5 days per week, for two years).
- Mineral wool material is biosoluble in the lungs and is rapidly cleared like all other nontoxic dusts, with no long-term health effects, due to its chemical composition.
- Mineral wool was categorized as not classifiable as to its carcinogenicity to humans (Group 3).
These toxicological exposure studies and the determinations of agencies like IARC, the American Conference of Governmental Industrial Hygienists (ACGIH), and the U.S. National Toxicology Program hold more weight in the world of regulatory toxicology than many people understand. Human epidemiological and animal exposure studies provide the scientific basis for determining whether a material is toxic. This large body of studies and the ultimate IARC determination removed mineral wool material from all lists of possible human carcinogens worldwide.
In addition, 10X superoxalloy is the only bio-soluble abrasive available. There are no regulations for disposal and shipping, making it easier to transport and remove from your jobsite.
Choose a Safer Abrasive Media for Your Next Project
Abrasive blasting is a crucial process in many projects. However, it is essential to choose a non-toxic blasting media and follow all the relevant safety protocols to limit the health hazards of sandblasting.
10X Engineered Materials has made it our mission to provide safer abrasives to match a variety of project specifications. Switching to one of our abrasive media products will help you achieve superior results while protecting your workers’ health. Learn about our various products or get in touch with one of our experts for personalized support!