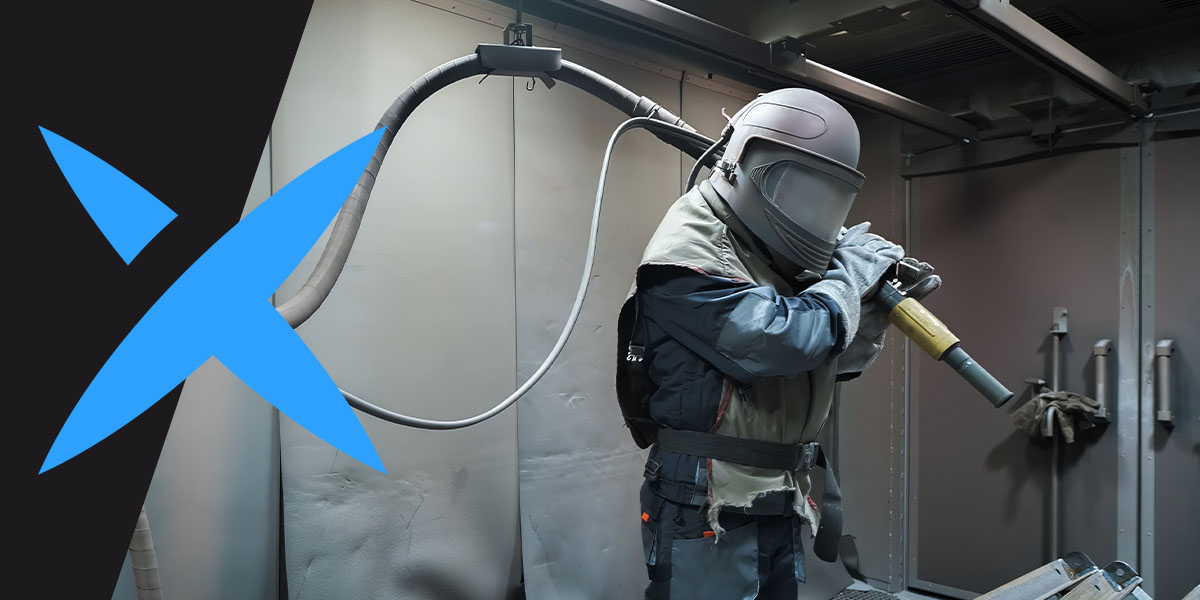
Sandblasting and soda blasting are abrasive blasting techniques used in cleaning and surface preparation. Although these materials follow similar processes and use the same equipment, they differ significantly in terms of their application methods, ideal use cases and abrasiveness.
Understanding these differences, including soda blasting media and the sandblasting vs. soda blasting process, will help you select the right technique for your project based on material and desired finish.
Understanding Sandblasting
Sandblasting, more commonly referred to as abrasive blasting or media blasting, is a process that uses a stream of abrasive materials, propelling them at high velocity against a surface under high pressure. It delivers a similar result to manually sanding a surface but much more quickly than manual sanding. Common applications include:
- Cleaning and restoration: Sandblasting can be used in architectural restoration and cleaning monuments and building facades.
- Industrial cleaning: It’s a crucial technique in industrial settings, as it cleans molds, machinery, and equipment without damaging underlying surfaces.
- Surface preparation: Industries like shipbuilding use sandblasting to remove contaminants and prepare metal surfaces for coating or painting.
- Artistic applications: Sculptors and artists use sandblasting to create intricate designs on stone, glass, and metal surfaces. This technique allows for precise etching and detailing.
- Polishing and deburring: Manufacturers use sandblasting to remove sharp edges and burrs from metal parts, achieving smoother finishes and ensuring product quality.
The process typically uses abrasive materials like garnet, aluminum oxide, steel grit, or silica sand, depending on the required surface type and level of abrasiveness. Some of these materials pose serious health risks to operators, as prolonged exposure can cause diseases like silicosis.
What Is Soda Blasting?
The soda blasting process is an abrasive blasting technique that uses sodium bicarbonate or baking soda as the blasting media. The process uses a significantly lower pressure than sandblasting. It involves propelling fine sodium bicarbonate particles at high velocity using compressed air. Specific applications of this process include:
- Graffiti removal: Soda blasting is a non-destructive method for removing graffiti from stone, brick, or other delicate surfaces without altering the substrate.
- Automotive restoration: Soda blasting is used to strip paint from car bodies, especially for antique or classic vehicles. It removes old paint without causing heat buildup, preventing sheet metal warping.
- Fire damage cleanup: Soda blasting can effectively deodorize and remove soot, stains, and smoke from metal, wood, and masonry surfaces after fire damage.
- Food and beverage industry: Soda blasting is often used to clean food processing equipment, as sodium bicarbonate is a nontoxic material that doesn’t leave harmful residues.
Sodium bicarbonate is a fragile material that creates dust during use as the material breaks upon impact. Operators must wear respiratory protection to protect their lungs.
Soda Blasters vs. Sandblasters: Main Differences
How are sandblasting and soda blasting different? Both sandblasting and soda blasting have specific properties that influence how they interact with various surfaces, the types of projects they excel in, and their overall efficiency. Understanding these distinctions is crucial for selecting the appropriate method to achieve your desired results.
- Abrasive materials: Sandblasting uses various abrasive materials based on their hardness and size, influencing their cutting power. Soda blasting uses sodium bicarbonate as the blasting medium. It’s softer than typical abrasives.
- Surface impact: Sandblasting is highly effective for cleaning and stripping hard surfaces to remove tough industrial coatings. However, it can cause pitting or surface deformation in softer surfaces. Soda blasting has a mild impact, making it suitable for chrome, glass, and thin sheet metal. It’s ideal for preserving the integrity of thin metal panels.
- Cost and application comparison: While sandblasting is faster and typically more cost-effective, soda blasting is a better choice for many applications where the goal is only to clean the surface. However, if you need to leave a profile on the surface of the metal substrate, blasting with a harder abrasive will be necessary.
- Efficiency: Sandblasting offers high efficiency, especially in surface preparation. Soda blasting abrasives can’t be reused, and the process often requires extensive cleanup time and equipment.
The Unique Benefits of Sandblasting
Deciding when to use sandblasting is crucial for the success of a surface preparation or cleaning project. At its core, the choice depends on the surface characteristics, the extent of the material that needs to be removed, and the overall project scope. Sandblasting is the better choice when you are dealing with:
- Hard surfaces: It’s ideal for use on durable materials like concrete, iron, aluminum, and steel, where surface damage is less of a concern.
- Large-scale projects: When speed is key, especially on larger surface areas, sandblasting’s ability to quickly remove paint, coatings, and contaminants makes it more cost-effective.
- Heavy rust: Sandblasting’s higher abrasiveness or cutting power makes it suitable for removing old paint, stubborn rust, and industrial coatings.
About Superoxalloy Abrasives
Superoxalloy abrasive is an engineered alloy made of oxide materials. High heat and rapid cooling create noncrystalline or amorphous particles that stay intact despite the stress of high-speed mechanical impact imparted on the particles during abrasive blasting, resisting breakage up to 120 PSI or higher. This abrasive creates extremely low dust levels, and its polymorphous particles perform multiple blasting steps in one pass, reducing the number of surface preparation steps.
Superoxalloy abrasive products include:
EpiX
EpiX is a finer mesh sandblasting media available in enhanced profile (EP), medium profile (MP), and low profile (LP). This product significantly reduces dust and processing time, making it a cost-effective blasting abrasive. For example, EpiX EP removes powder coating in only 20 seconds — which is over two minutes faster than aluminum oxide.
KinetiX
KinetiX is an innovative solution for optimizing surface preparation. This product is available in KinetiX-20/70 grade for common blasting applications and will produce a profile in mild carbon steel ranging from 2.5 to 3.5 mils deep. KinetiX-40/70 grade is more appropriate for thinner coatings. It helps you take on high-volume projects like large production or maintenance jobs while still promoting environmental safety, and this product will produce a profile in mild carbon steel ranging from 2.0 to 3.0 mils deep.
DynamiX
DynamiX is a heavy-duty grade superoxalloy abrasive often used in shipyards, rail car maintenance, on bridges, and pipelines. It quickly removes tough coatings, making this ideal for demanding tasks. This product delays rust bloom and has very low embedment while promoting worker and environmental safety.
Choose Safe Sandblasting Media With 10X Engineered Materials
While both techniques use high-pressure abrasive particles to remove unwanted materials from surfaces, they have unique characteristics that make them suitable for different applications. Soda blasting has a gentler approach to surface preparation and is well-suited for delicate materials. Sandblasting gives you power and efficiency, especially for heavy-duty applications. However, when using the right abrasive material, you can use sandblasting for many surfaces and even the toughest coating remmoval blasting jobs.
10X Engineered Materials offers the market’s only biosoluble blasting abrasive, delivering a high-quality finish. Our products are SSPC AB-1 Certified, California Air Resources Board Approved, and NAVSEA Military QPD: MIL-PRF-22262C listed and approved.
Make an engineered decision and choose superoxalloy abrasives. Shop our range of superoxalloy abrasives today and enjoy free technical support for your projects.