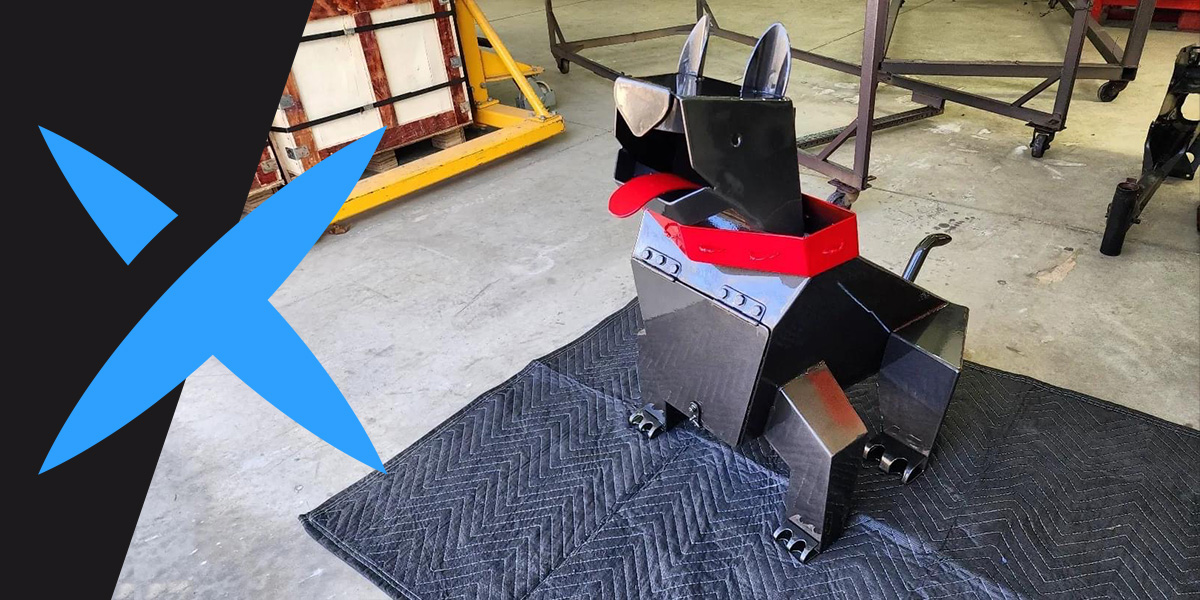
Will Sandblasting Remove Powder Coating?
Sandblasting, thermal, and chemical burn-off processes are often used to remove powder coating. Sandblasting is also a common method for preparing a surface for new powder coating. To sandblast a surface, you can use an air compressor to send abrasive grains at a high velocity toward the metal surface or substrate.
However, more advanced blast abrasives — such as EpiX superoxalloy abrasives from 10X Engineered Materials — can save you time and money. By using EpiX, it is often possible to eliminate the need for thermal or chemical burn-off processes. Keep reading to learn more about the best option for removing powder coating.
What Is Powder Coating?
Powder coating is a type of coating that is applied as a free-flowing dry powder, which can create a protective finish on a variety of different materials like aluminum, steel, and even stainless steel. It’s versatile, durable, cost-effective, and an environmentally friendly coating. Because there are a wide variety of color and texture options, it’s also aesthetically pleasing. High-end automotive wheels are often powder-coated.
Unlike wet paint, powder coating is applied with a spray gun and electrostatic charge. After being painted, components are put into an oven to cure.
This type of finish is extremely high-quality and is applied to objects as varied as playground equipment and kitchen utensils. It may also be used to protect heavy machinery and manufacturing equipment from corrosion.
Best Abrasive to Remove Powder Coating
With enough time and use, powder coatings begin to wear away and become less effective. A good way to remove these coatings and start anew is by using abrasive blasting, commonly referred to as sandblasting. Several blasting abrasive materials are commonly used for this purpose, including:
- Aluminum oxide
- Glass beads
- Garnet
These blasting materials are all capable of removing powder coating so new paint can be applied. They have many benefits; some work quickly and have been the standard abrasives in the blasting industry for decades. However, there are a few things that can be improved beyond what these traditional blasting materials are capable of.
For example, aluminum oxide is often more expensive and slower than other abrasives on powder coating removal, which makes it incredibly important to use a blasting room/cabinet to recycle it for future use. Aluminum Oxide struggles to cut through powder coating; it often heats it up, and the coating acts like a rubbery material resisting abrasion based removal. After several uses, the aluminum oxide particles will become finer, making them less effective.
Some of these abrasives can be harmful or damaging to the operators. For example, when inhaled, actual sand can contain high amounts of crystalline silica, which causes serious health issues such as lung inflammation and silicosis. Other alternatives, like aluminum oxide, garnet, coal slag, copper slag, nickel slag, and crushed glass, can also be harmful in various operating conditions.
Alternative Methods to Remove Powder Coating
Other common methods for removing powder coating include chemical strippers or a thermal burn-off oven, as mentioned above. Unfortunately, those methods can be dangerous, expensive, slow, and difficult to manage.
For example, some powder coat strippers, like chlorinated hydrocarbon phenol acid blends, commonly referred to as ‘chemical strippers’ can burn your skin on contact, are difficult to handle safely, and often have intense and harmful off-gassing. The intense heat from burn-off ovens may alter or weaken the underlying metal, warping the structure or making it unable to achieve a proper finish with a new coating.
The Best Blasting Media for Removing Powder Coatings
There are various abrasive blasting medias available for removing powder coating from surfaces, such as aluminum oxide, garnet, and 10X’s superoxalloy, but not all of them will work on certain surface types.
The choice of media will depend on many factors, including:
- Surface hardness
- Desired surface finish
- Surface condition
- Compatibility of media with the specific coating’s chemistry
- Type of coating removal equipment available
However, there is a prime option for removing powder coatings — an option that is both cost-effective and durable for any project. That option is superoxalloy blast abrasives. This type of abrasive has been specifically formulated and engineered to achieve optimal blasting performance under a wide variety of conditions.
Choose Superoxalloy Blast Abrasives From 10X Engineered Materials
The EpiX superoxalloy blast abrasives from 10X Engineered Materials quickly and effectively remove powder coating and also leave a clean SSPC SP-5 white metal surface finish, virtually free of embedded particles — so the next coating can be applied correctly. In many cases, you can skip the need for chemical stripping because this abrasive does such a thorough job.
On top of all this, it is much safer than blasting with garnet or aluminum oxide. Superoxalloy abrasives are low dusting and biosoluble; click here to learn more about the safety advantages of superoxalloys. They can even be recycled and reused many times, and they are a sustainable 100% recycled product.
To learn more about these superoxalloy blast abrasives, reach out to us at 260-253-2278 or fill out our online form!