Asphalt milling machines, often called “road eaters,” rely on one critical component: their milling bits. These bits endure extreme forces during operation and eventually wear down. Once worn, the bases to which the bits are attached are removed and sent to manufacturers for refurbishment. This involves attaching new tungsten carbide tips to the bases to restore their functionality. However, proper base preparation is essential to ensure a strong bond and a long service life for the refurbished bits.
10X Engineered Materials was approached by a manufacturer experiencing higher-than-acceptable in-service failure rates. Their previous process involved:
- Blasting with silicon carbide for 30–60 minutes.
- Flux cleaning to prepare the base.
- Brazing to bond the base and tip.
The quality of the bond was tested using a reverse press, measuring the PSI at which the bond failed. Under the old process, bonds typically failed at pressures between 5,000 and 8,000 PSI, highlighting significant room for improvement.
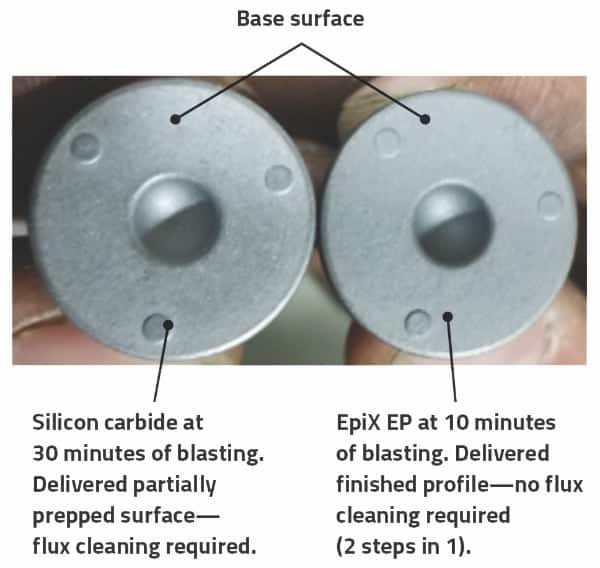
When the manufacturer switched to our EpiX EP abrasive, the results were transformative:
- Blasting time dropped to just 10 minutes, cutting production time dramatically.
- The flux cleaning step was entirely eliminated, simplifying the process and reducing costs.
- In testing, the bond strength improved so significantly that the bond itself never failed. Instead, the tungsten carbide tips shattered under pressures exceeding 18,000 PSI—a clear testament to the superior bond strength.
Finished Part
Tungsten carbide asphalt milling and removal bit.
10X Abrasive
Bond withstood 18,000 PSI with EpiX surface prep – the tungsten carbide broke before the bond.
Silicon Carbide
Bond failure at 5,000 PSI with silicon carbide surface preparation.
Ready to See the Difference 10X Can Make? Switch Today!
This improvement underscores the power of 10X engineered materials. By upgrading to EpiX EP, manufacturers can achieve faster processing times, lower costs, and exceptional performance in the field.